
Lone Star State growers and greenhouse operations are picking up the pieces after an unexpected mid-February winter blast saddled producers with in an estimated $600 million in agricultural product and revenue losses, according to initial estimates from Texas A&M AgriLife
The biggest hits were taken by the state’s most prominent field crops — citrus, cotton, trees and shrubs and vegetables — but nearly a fortnight of below freezing temperatures felt as far south as Brownsville, Texas, also damaged many of the state’s nurseries, garden centers and greenhouse operations.
“The green industry will experience increased labor, fertilizer and other costs as part of the price of replacing the plant material that was lost during the winter storm,” said Marco Palma, Ph.D., horticultural marketing expert in the Department of Agricultural Economics.
“The green industry has had severe damage, especially in some of the larger metropolitan areas such as Houston, Dallas, San Antonio and Austin,” adds Amy Graham, president and CEO of the Texas Nursery and Landscape Association (TNLA). “We have a lot of nursery plant growers in East Texas and quite a few of them have reported total losses. In some cases, complete greenhouses collapsed. In other instances, plants died because there was no propane for heating greenhouses.”
Here are a couple stories of survival from Texas green industry operations:

How they prepared
Ben Van Wingerden, Color Orchids’ founder and CEO, recently relocated to Texas to help open a new southern production greenhouse. Call it a stroke of foresight genius, or perhaps it was mere coincidence, but Van Wingergen and Co. made the prudent decision to outfit their structure for the same climate and weather conditions they dealt with on the Eastern Seaboard. That decision paid off big-time this winter.
“The builder, Prins Usa, built the greenhouse here as if it were located in Virginia,” Van Wingerden explains. “We engineered with a 3-foot snow load on the roof, and all the walls are insulated panels. All our water lines are buried deep enough to avoid freezing. And we put in natural gas lines and a backup fuel source, and we also have a 400-kw generator.”
Even with all those precautions in place, the team at Color Orchids remained concerned as they monitored the weather forecasts and planned for the coming storm. Orchids are, according to Van Wingerden, notoriously sensitive to temperatures below 65° F.
“Our biggest concern was the extremely low temperatures, because when you build new, you size your boiler based on a certain outside temperature in relation to your desired greenhouse temperature,” he recalls. “Orchids are sensitive, and the temperature can’t fall below 65. When I was designing the facility, I picked an outside temperature of 12° F for the lowest temperature it can get.”
So, the facilities’ boiler for heating the greenhouse was sized and installed, and a backup boiler for “redundancy and expansion” was also added into the mix. Still, even with all those precautions in place, something continued tugging at Van Wingerden.
“I was concerned that if one boiler went out, then the backup boiler would have trouble maintaining the proper temperature,” Van Wingerden says. “So, that meant everyone had to remain on standby in case a boiler decided to go out on us.”
The crew also fired up and monitored the facilities’ backup generator in the runup to the storm.
“We also wanted to confirm that the generator had been properly winterized by the company that services our generator for us, and then we just went around and insulated everything outside with foam, hay, and covers, that we thought could freeze.”
How they fared
Color Orchids, known in the industry for its Simple Shot and Simple Wick watering systems, thankfully came through the storm and subsequent power outage virtually unscathed, according to Van Wingerden.
“The end result of all of this, for us, was a big win,” he says. “Of course, you do lose growing days, but in the scheme of things that is nothing compared to what could have happened. Our structure held up, we kept the power on, and we didn’t lose our crop.”
Where a lot of Texas-based horticultural operations saw big problems during Uri was with freezing and malfunctioning irrigation lines, storage wells and systems. ColorOrchids came through cleanly in that regard, as well.
“We treat our well water for irrigation water, and we use a storage tank which is kept inside the greenhouse, so we did not encounter any irrigation issues,” Van Wingerden says.
How things look for 2021
It’s the question on the tip of everybody’s tongue down in Texas. How will plant availability be affected? Will the new plant parents still be able to seek out and grow all of the varieties they want this spring?
“I think that will be interesting to see,” Van Wingerden says. “I just read an article claiming the state will suffer around $600 million in ag product loses. We have already heard from our neighbors and partners around the state that there are some places being affected pretty badly, but I couldn’t tell you what kind of impact it will have overall yet.”
One prediction he will make, however, is any disruption will likely exacerbate some of the supply chain issues the industry felt in recent months.
“There was already a large disparity between supply and demand right now in our industry, so any additional shortage will just widen that gap, and it should drive prices up,” he says. “If I had to make a prediction, I would say the retail stores will continue this trend of increased sales of everything plant-related, and these stores will be searching high and low for product to put on their shelves.”
What they learned
Always have enough back up fuel and energy sources, Van Wingerden advises.
“It’s honestly not a huge up-front investment, and I was very happy that we could switch to propane if natural gas prices got to high, and we could run the generator if our kilowatt price went up to high,” he explains. “Well, that happened. In some cases, the electric companies in the state [Texas public utilities are deregulated] were charging 650x their normal kilowatt price. For us, that would’ve been an over $1-million electric bill.”
How they prepared
Native Texas Nursery grows ornamental crops, perennials, shrubs and young trees for wholesale dealers and distributors both in the field and under cover. The wholesale plant producer leverages 28 single layer poly covered cold frame “greenhouses” as well as a modern, double gutter connected propagation greenhouse.
According to owner Bill Carson, the operation has about 31 propane heaters — one for each cold frame as well as three staged throughout the propagation greenhouse — it relies on in the cold months to keep the crops above freezing and in vegetative growth mode.
“Our lifeline during the winter is keeping the propane coming,” Carson says. “We have about 3,000 gallons of storage capacity on site, and we have a very good propane supplier who will make regular trips to top us off during the cold months.”
The cold frames covered with poly that protect its perennial crops are maintained around 45° F, while the propagation house needs to keep a steady 60° F baseline to keep those young plants viable and developing.
“We knew from the forecasts that we were facing a long stretch of single digit temperatures, and when we get down to single digits, we tend to use about double the propane we’d normally need,” Carson says. “The storm was set to arrive on a Sunday, and the Friday prior, I did the math and went into a panic.”
Carson crunched the numbers and came away confident that the operation could handle three to four nights of single digit temperatures without completely running out of propane.
“We could handle four, but not five, not six nights in a row, and on top of that, a six-inch snow accumulation as well,” he explains. “When we get that much snow down here, everything shuts down and nothing moves anywhere — there’s not a single snowplow in this town. Well, this was going to stick around for six days, and our last propane delivery was on Saturday.”
Before that final load of propane arrived, Carson huddled up with his supplier and drew up a plan of attack: with travel set to shut down across the state for a few days at the very least, the propane supplier could lend Carson a 3,500-gallon tanker, full of propane, to keep on site in case they ran out during the week. The rep even came out and trained some of Carson’s crew members how to operate the tanker, and how to offload the propane into their storage tanks as needed.
How they fared
Due to the quick thinking and collaboration of Carson and his propane dealer, the operations lost very few plants during the storm.
“That was about 7,000 gallons of propane [delivered] that we got in here quickly, now that is what I call service,” Carson beams. “I shudder to think about what would’ve become of us if we did not have enough fuel to keep the heaters on.”
Keeping the heaters running was just the start of it, though. Carson had his crews staged around the clock to monitor fuel levels throughout the week, since 32 propane heaters all running at the same time can really chew through some fuel, fast. Then, once the snow itself arrived, the workers climbed atop the gutter-connected propagation house and shoveled the snow to keep it from collapsing the poly covering.
“Between what our propane guy did, and what our amazing staff did during the storm, we were able to save about 95% of the product, and that 5% of loss was a lot of the really young and tender stuff,” Carson says. “And now, we’re shipping out product like crazy.”
Pressed to take an educated guess at the level of losses the operation would have suffered, Carson says you have to measure in both dollars of product lost, as well as time and future product potentially ruined.
“It would have been in the excess of a couple million dollars of losses, and if we would’ve lost a bunch of plants in our propagation house that would’ve crippled us for at least another year on our tree crops,” he says. “Just the labor costs alone of having to remove and destroy all that material, with no new revenue coming in, would’ve been disastrous. It basically would’ve shut this company down for good.”
Native Texas’ unique approach to plant sourcing — the operation does not order genetics from seed catalogues; all of its varieties are sourced in the wild (hence the native moniker) — makes sourcing replacement plants quickly a virtual non-starter. The operation, with 50 full time workers, would have had to shut down and lay off its crew until fall, when it could get back to sourcing native plant seed.
“We would’ve had to let go of virtually all of those employees, it would’ve been a shell of a company compared to what we are today,” Carson says.
How things look for 2021
Of course, anytime you lose any amount of plants, it’s uncomfortable. Yet, considering the relatively minor losses that Native Texas experience compared to some of their Lone Star State neighbors, prospects for the next few months are looking up.
“We’ll take a bit of a hit, and it will take some real hard work for us to overcome that, but we’re relatively speaking in a pretty good place right now,” Carson says. “We have greenhouse material that is ready to ship out now that will bring in some immediate cash flow for the business.”
What they learned
Native Texas’ winter storm Uri experience certainly calls to mind the old saying: “an ounce of prevention equals a pound of cure.” By preparing before the storm hit, the team avoided some of the catastrophic losses others nearby in the green industry suffered.
That is a valuable lesson, whether you’re staring down a once-in-a-lifetime weather event or another Mother’s Day weekend mega-rush down at the garden center.
“We were prepared for this cold, but the amount of snow and just how long it stuck around, we couldn’t have been prepared for that. I’ve been in this business for 35 years and nothing that I’ve witnessed has approached the scale of this,” Carson says, noting the operations facilities spent a record 140 hours in a row below freezing.
Carson foresees a few notable developments coming out of this tragedy.
“People that are growing outside exclusively, I think they will really be looking hard at making some changes going forward,” he says. “For us, we will prepare better for propane pressure problems, we’ll probably add more storage tanks as well. And I think we’ll add some more backup heaters. My crew can hook those suckers up in just under 15 minutes. We’ll have brand new ones still in the box, ready to go when we need them.”
The greenhouse structures companies will surely be making some sales calls down in Texas this summer when the busy season winds down.
“I think that’s fair to say, more people down here will probably think a bit longer and harder about growing in a greenhouse, and we’re talking about adding more greenhouses here, too,” Carson admits. “But, at the end of the day we consider ourselves farmers, and farmers are always at the whims of the weather.”
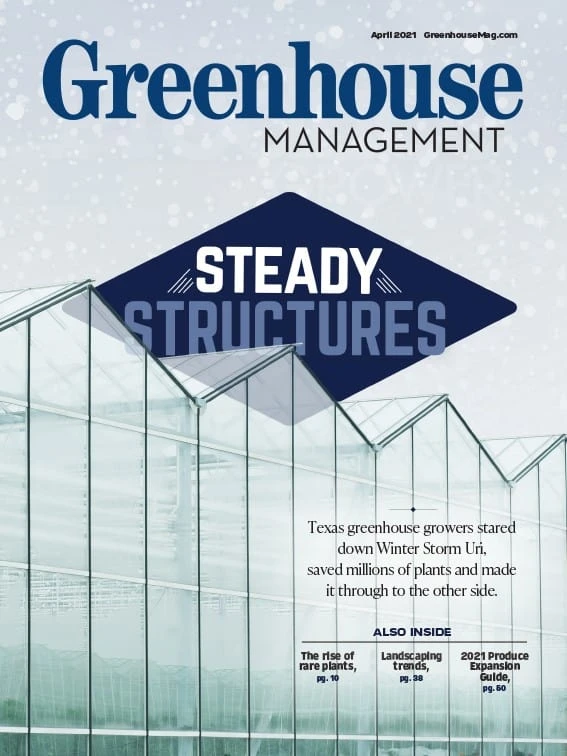
Explore the April 2021 Issue
Check out more from this issue and find your next story to read.
Latest from Greenhouse Management
- CEA Alliance celebrates bipartisan introduction of Supporting Innovation in Agriculture Act
- Dümmen Orange North America celebrating 25th anniversary in 2025
- CEA HERB Part 1: Best management practices for culinary herbs
- Lawsuit challenges new H-2 visa rules
- CEA HERB Part 2: A guide to increasing the sowing density of culinary herbs
- Illinois Landscape Contractors Association changes name to Landscape Illinois
- 2025 Proven Winners Horticulture Scholarship applications now open
- ICL’s Gemini Granular herbicide now registered for use in California