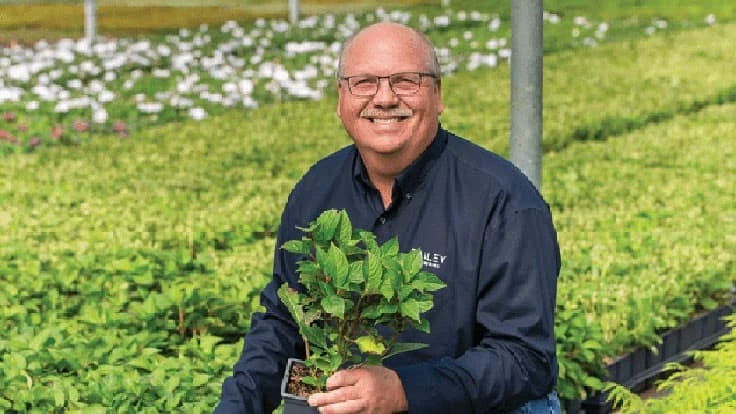

Dave Gross has grown plants practically his whole life. “I’ve been working in the garden since I could walk,” he says. By age 11, he already had his first job in the industry, helping his priest start a small retail greenhouse where they grew bedding plants.
He went on to study botany and landscaping in college, where Bailey Nurseries recruited him as an intern. By the time Gross joined Bailey Nurseries full-time in 1981, although he was only 21, he already had 10 years of growing experience — making him a prime candidate to launch and lead the nursery’s bedding plant operation. In 1991, after 10 years as foreman of production and growing, Gross was promoted to his current role as production manager at Bailey’s Nord Farm facility in St. Paul, Minnesota.
The site, which covered about three acres when Gross first joined the company, now spans 22 acres under cover plus two acres of outdoor production. As his responsibilities have evolved from growing plants to cultivating a team of people, Gross developed processes along the way to streamline production and optimize his team. Here’s how he’s contributed to the operation’s growth over the last 40 years.
Simplifying the crop mix
At its peak, Nord Farm employed 240 people producing a diverse variety of crops — from bedding plants to potted Jumpstarts® liners, bareroot cuttings, flowering Bud & Bloom containers and more. Over time, Gross says, the bedding plant program alone grew to about $5 million in sales. “It got to the point that we had so many products and so many pot sizes that our supervisors were overwhelmed,” says Gross, who oversees 11 supervisors at Nord Farm. “At that point, I said, ‘This isn’t going to work. There’s got to be better crops we could grow.’”
Gross led a cross-functional team to determine the program’s fate, and they confirmed that the labor-intensive bedding plant operation wasn’t making the most efficient use of Bailey’s greenhouses. They discontinued the program in 2015, ultimately repurposing the greenhouses to increase production of Bud & Bloom hydrangeas and Jumpstart liners.
“What we’ve done is change our product mix to require less staff and [maintain] higher profit margins,” he says. “Now we’re filling the same space, and this year, we topped out at 110 people, versus 240. We’re trying to simplify by reducing SKUs, pot sizes and varieties in order to be more efficient.”

Prioritizing the process
Gross learned another important lesson in 2015, when an experienced key supervisor left the company. “I realized I didn’t know his job as well as I should have. I didn’t know his timetable of what he did, why he did it or when,” Gross says. “So, I decided to record every significant process related to production, when it began and when it ended.”
Initially, Gross started documenting these jobs — like taking cuttings and winterizing greenhouses — every week on the whiteboard. Ultimately, these timetables were transferred down on paper so the team could easily reference the schedule. Every week, he communicates constantly with his team to explain their priorities as they progress toward short- and long-term production goals.
“When I decide to retire, somebody can step in and look back since 2015 and know what happened every week of every year,” Gross says. “Communication is a critical piece of what I do because everybody needs to understand the priorities. If everyone understands what has to get done, they share the labor willingly.”
Innovating production
In addition to inventory simplification and clear communication, Gross also relies on automation to make his team more efficient. While Bailey is “not as automated as many large growers because of our diversified crops,” he says, he works closely with an in-house fabrication team to develop customized equipment that makes moving, pruning and harvesting plants easier.
For example, “Growing high-quality rooted plugs and liners requires consistent pruning, and we achieve that with multiple mowing devices,” Gross says. “We have five-wheeled mower frames that move two bagging mowers up and down the greenhouse. One person can [prune] a house in four hours. We just motorized one of them, where you can take a joystick and a remote control to run the mower without even pulling it.”
Bailey’s fabrication team similarly modified a plant lifter onto a specialized tractor to help the growing team streamline harvests. “We can harvest a hundred thousand cuttings in two hours with four people,” he says. “It’s a very efficient system.”
These process improvements help Nord Farm produce over 10 million plants per year as Gross cultivates an efficient, effective growing team.
“Over the years, I’ve been involved in [the production of] tens of millions of plants. To watch an unrooted cutting turn into a rooted plant in a larger container, and then finally to see your retail product looking good on display for the end-user to take home, that’s a great feeling,” Gross says. “It’s satisfying to grow plants, but if we can grow our people, that’s my biggest satisfaction.”

Explore the November 2021 Issue
Check out more from this issue and find your next story to read.
Latest from Greenhouse Management
- USDA fires experts on invasive pests, including Asian citrus psyllid, chilli thrips
- CEA Alliance celebrates bipartisan introduction of Supporting Innovation in Agriculture Act
- Dümmen Orange North America celebrating 25th anniversary in 2025
- CEA HERB Part 1: Best management practices for culinary herbs
- Lawsuit challenges new H-2 visa rules
- CEA HERB Part 2: A guide to increasing the sowing density of culinary herbs
- Illinois Landscape Contractors Association changes name to Landscape Illinois
- 2025 Proven Winners Horticulture Scholarship applications now open