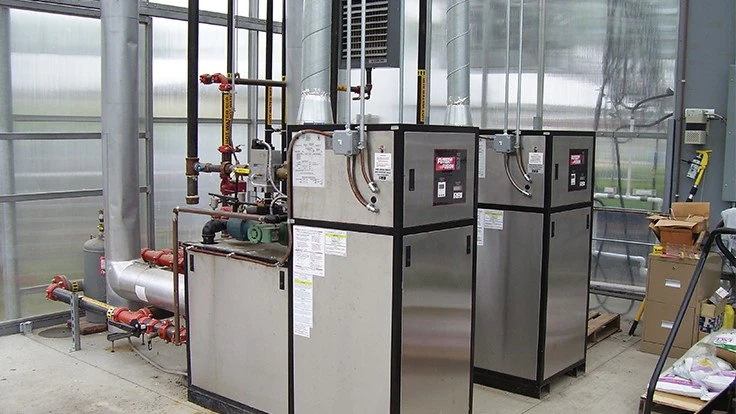
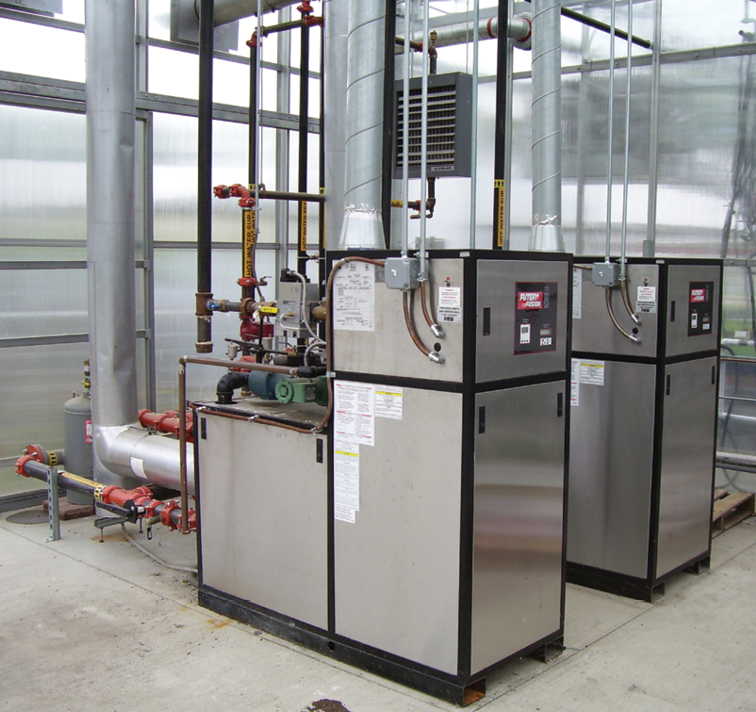
Have you had the efficiency of your heating system checked recently? In doing energy audits, I have seen efficiencies on old furnaces and boilers that were less than 70%. The fuel savings with a new unit having 90% or higher efficiency can have a short payback and also reduce typical maintenance problems that keep you up on cold nights. Most manufacturers now include condensing heaters and boilers in their product lines.
How is this high efficiency achieved as compared to conventional units that typically operate at 80 to 85%? When fuel oil, propane and natural gas are burned, steam is one of the byproducts. Burning 1 gallon of fuel oil will produce about 0.98 gallons of water, 1 gallon of propane about 0.82 gallons and 1 ccf of natural gas about 1.16 gallons. In a non-condensing boiler or furnace, this water vapor, which has a temperature of 400 to 500°F, along with the other byproducts, normally goes up the stack and is exhausted into the atmosphere. The high temperature is needed to avoid excessive flue condensation or damage to the boiler from the acidic condensate.
A condensing boiler incorporates an extra heat exchanger in the flue gas exhaust system so that the water vapor condenses back to a liquid. This process captures up to 8000 Btu of heat per gallon of condensate, which is as much as 13% of the original fuel energy. The condensate heats the incoming air (if an air to air heat exchanger is used) or pre-heats the water (if an air to water heat exchanger is used). After the heat is removed, the low-temperature condensate water can be drained through a corrosion resistant pipe (usually PVC), eliminating the need for a chimney.
Condensing boilers have to have low return water from the radiators to work best. With water at 130°F, 15% of the water vapor will condense, whereas at 60°F, over 90% of the water vapor will condense. A root zone system with return water at 80 to 90°F is a good example of where it will work well.
The efficiency is also affected by the humidity of the air. Under the right operating conditions, condensing boilers can achieve an efficiency of 95% or more.
Most heating units with condensing capability have modulating burners that are capable of multiple firing rates. By using embedded control, the firing rate is matched to the heat load needed to give best performance. This means that at high firing rates, the efficiency may decrease but never be less than a conventional boiler.
Today's boilers are much smaller than the old standard units as they have much less water in the jacket. They are self-contained so that much of the wiring and plumbing is done before you receive it. This reduces installation time considerably.

Avoid too large a boiler
Oversizing a boiler can reduce efficiency as the object is to have it run continuously. This is done by adjusting the firing rate — low fire when minimum heat is needed and high fire for the coldest weather. Cycling decreases efficiency from start-up and shut-down operation and increases wear on the boiler. To get the greatest benefit from a condensing unit, it is better to size the boiler for an average winter temperature, not the normal coldest temperature frequently used by engineers. The more continuous operation will keep up with the heat needs better than a unit that cycles.
For condensing hot air unit heaters that only have one firing rate, staging multiple heaters to operate at different temperatures can provide a more uniform greenhouse temperature and save fuel. HAF air circulation can be used to keep a uniform temperature in the greenhouse.
Provide adequate radiation
Typical non-condensing boiler systems are usually designed for 180°F water temperature with fin radiation having an output of about 600 Btu/linear foot.
With condensing systems, additional radiation is needed to provide the needed heat. PEX tubing in the floor, low output fin under the benches or overhead or root zone heat on the benches is commonly used to get the required heat. Installing a condensing boiler with your present radiation system will probably not provide the savings you expect.
Although condensing boilers and heaters are more expensive than conventional units, the greater efficiency can offset the additional cost. USDA Natural Resource and Conservation Service funding may also provide an incentive to make the change.
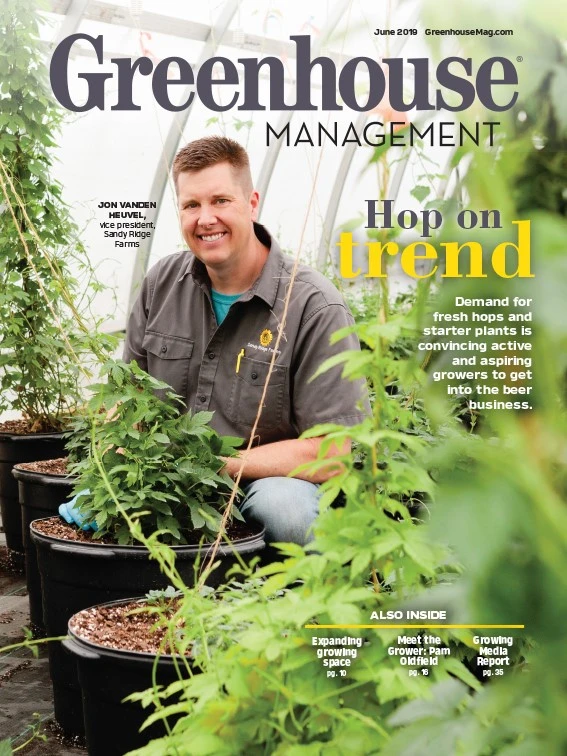
Explore the June 2019 Issue
Check out more from this issue and find your next story to read.
Latest from Greenhouse Management
- Pennsylvania Horticultural Society shares top gardening trends from 2025 Philadelphia Flower Show
- California Spring Trials 2026 dates announced
- Les Evans promoted to DRAMMwater segment manager, Al Zylstra to retire
- Hoffmann Family of Companies to acquire N.G. Heimos Greenhouses
- GIE Media Horticulture Group wins five regional 2025 Azbee Awards of Excellence
- Grant awarded to test western U.S. wood species for use as wood fiber potting substrate
- Pennsylvania Horticultural Society announces 2025 Gold Medal Plant winners
- Oasis Grower Solutions announces new Southeast territory sales manager