

One low-cost method of increasing growing space without building new greenhouses is to install a roll-out tray system. A roll-out system doubles growing space by placing one layer of plants on the floor and a second layer 20 to 30 inches above the floor on a rail system. During the day, the trays are rolled outside the greenhouse onto a matching rail network. Both crops receive full sunlight. At night, they are rolled back into the greenhouse. This system can be adapted to both hoophouses and gutter-connected ranges. It does, however, require a level area adjacent to the greenhouse.
The system works well in the busy spring season. It is good for hardening off bedding plants, perennials and herbs during the spring and for potted plant production during the fall. It has been used for growing cool season vegetables too, including arugula, lettuce, spinach and more.
Some growers have also used the roll-out system as an intermediate step until funding is available to build a new greenhouse. The greenhouse can be built directly over the roll-out supports. It just takes planning to make sure that everything fits together.
If designed properly, the trays can be moved from either the greenhouse or the roll-out area to the work area for planting or shipping operations. This requires a pipe transport rail system and transfer stations to change direction. Compressed air is used to raise or lower the tray to change direction.
Although I have seen movable trays as large as 10 by 50 inches, the usual size is 4 to 6 inches wide by 8 to 16 inches long. This makes for easy moving. When placed on rails, labor is saved too, as a whole row of trays can be pushed in or out at one time by one person. A typical design is to install two rows of trays in a bay or hoophouse with an access aisle in the middle. These can be moved sideways on the rails to allow access to an individual tray.
There are several variations in bench design. An aluminum extrusion frame with a galvanized expanded metal bottom is the most common material for weight and long life. The bottom needs to be supported on 24-inch frame to prevent sagging. There is little maintenance to these trays.

Welded steel, although heavier, is another available option. Molded plastic trays or inserts are used when a watertight tray is needed.
In the roller conveyor system, flat bottom trays that ride on trolley wheels or fixed casters attached to support rails are used. In a second system, the rollers are attached to each tray and ride on the smooth pipe rails.
The support system is usually made of galvanized steel tubing. The rails are welded together to form a smooth surface. Support posts are placed in concrete piers or fastened to a concrete walkway for rigidity. The system has to be strong enough to carry the weight of the trays, as much as two tons/tray. Bracing is needed to keep the system rigid when the trays are being moved.
A roll-out tray system can help harden off plants during the spring and grow cool-season vegetables.
The endwall of the greenhouse needs to be modified by installing doors that open to allow the trays to pass through. These doors can be manual as they are opened only once or twice each day.
Depending where your business is located, a roll-out tray systems can add valuable growing area at a time when it is at a premium.
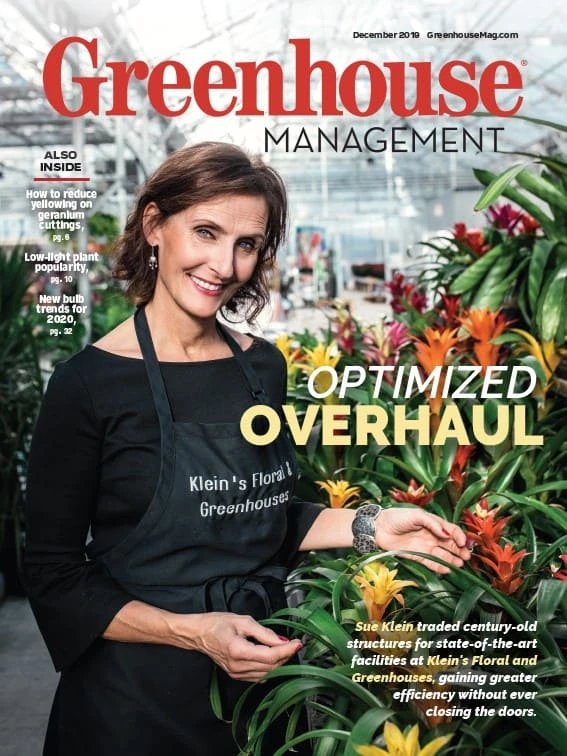
Explore the December 2019 Issue
Check out more from this issue and find your next story to read.
Latest from Greenhouse Management
- 2025 Proven Winners Horticulture Scholarship applications now open
- How to improve inventory and shipping management in the greenhouse
- Leading Women of Horticulture: Anna Ball, Ball Hort, and Terri McEnaney, Bailey Nurseries
- GM CEA HERB Part 2: A guide to increasing the sowing density of culinary herbs
- GM CEA HERB Part 1: Best practices for producing culinary herbs in controlled environments
- USDA fires experts on invasive pests, including Asian citrus psyllid, chilli thrips
- CEA Alliance celebrates bipartisan introduction of Supporting Innovation in Agriculture Act
- Dümmen Orange North America celebrating 25th anniversary in 2025