
The backbone of an efficient greenhouse operation is the utilities consisting of the electricity, water and fuel supply systems. As the business grows, these need to be upgraded to handle the additional facilities and growing space.
Usually the first system to be overtaxed is the electrical system. As more equipment is added, more circuits are needed. I have been in greenhouses where some fans had to be shut off so the water pump could be switched on. In other cases, the lights dim down whenever a furnace starts.
Now is a good time to have the system checked by a licensed electrician. In most states, electrical work on facilities used by employees or the general public must be done by a licensed electrician. The electrician takes the responsibility and liability for meeting the necessary codes and is also responsible for getting the necessary permits from the building inspector.

Electrical service
The electrical service must be of adequate size to handle the load. It provides a safe entrance and disconnect for the electrical supply wires entering the building. It can also be the point where distribution and grounding take place. The electrical service may be as small as 60 amps for a single hoophouse to as large as 800 amps or more for a gutter-connected range with a headhouse full of equipment.
To avoid multiple base charges, a single electrical service should be installed to serve all the greenhouses and accessory buildings. The best location is a dry, easily accessible area. The utility room of the headhouse is a good choice. In small operations, it may be placed on an endwall in one of the greenhouses. In operations with many hoophouses, a central electrical distribution pole is the best location. Any overhead wires should be a minimum of 18’ so that equipment and trucks can pass underneath. Underground installation in conduit is better for all weather operation.
As you add more equipment, an existing service may become overloaded. If operating at 80% of its rated load for more than three hours, overheating may occur with the possibility of deterioration of the wire insulation. The electrician can calculate the load. A new supply should be calculated with a 25% buffer for additional equipment or expansion.
Grounding
All electrical systems used in greenhouse operations must be grounded. Grounding helps to limit high voltage from lightning or a fault in the lines. It also limits the maximum voltage to ground from hot wires. Grounding a system usually involves connecting to a metal water pipe system, a metal building frame or driving copper rods into moist soil.

Distribution system
Electricity is distributed from the service entrance through individual circuits to motors, lights, heaters, etc. Each circuit is protected by a circuit breaker that opens the circuit when an overload, short circuit or ground fault occurs. Each electrical circuit and its associated wiring must be sized to handle the maximum load of the equipment attached to it.
In large, gutter-connected greenhouses or in operations with many individual greenhouses, feeder circuits are installed to reduce the amount of wiring needed. For example, a 200-amp service panel may have several 60-amp feeder circuits connected to it, one for each hoophouse. At the end of each feeder circuit, a distribution panel with branch circuits serves the motors and lights in that greenhouse. Feeder circuit wire size and the circuit breaker must be adequate to handle this load.
Wiring
The National Electrical Code requires that the wire type have insulation to fit the application: wet, dry, high temperature, etc. Where high moisture and dust are present, such as a greenhouse, the code requires that the wiring be placed in conduit. Electrical Metallic Tubing (EMT) is a good choice as it is galvanized with an organic inside coating and easy to install with many fittings available. The conduit can be sized large enough to contain all the wires needed to serve one area of the greenhouse. Watertight electrical boxes and receptacles should also be included to keep out moisture and dust.
Ground-fault interrupters
A common question asked is whether ground-fault circuit interrupters (GFCI) are required. They can prevent serious shock to persons under certain conditions by limiting the amount of current that is received. They do not work well in the moist, greenhouse environment and result in frequent nuisance tripping that could affect the operation of vital equipment. A portable GFCI is recommended for persons using power tools in the greenhouse or outside in damp or wet locations.
Temporary wiring
I’m not sure why but as I travel around, I observe considerable makeshift wiring in greenhouses probably done by the grower or his staff. Circuit panels with the cover off, ungrounded circuits, unsupported wires, taped or untaped wire splices, outlet boxes without covers and outdoor wiring without mechanical protection are common. I think the intent is to complete the work after you are sure that the problem in the circuit is corrected or when you have more time. It frequently doesn’t get done. To provide safety to the workers or public these situations should be corrected quickly.
Get curated news on YOUR industry.
Enter your email to receive our newsletters.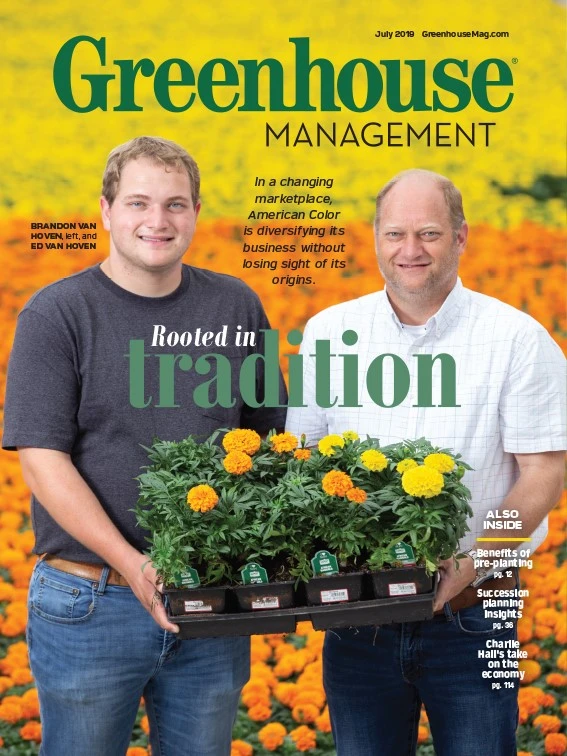
Explore the July 2019 Issue
Check out more from this issue and find your next story to read.
Latest from Greenhouse Management
- The Growth Industry Episode 3: Across the Pond with Neville Stein
- Trends: Proven Winners 2025 perennial survey shows strong demand
- Online registration opens for the 2025 Farwest Show
- Green Gear: Battery-powered backpack sprayer and a hoodie
- Sustainabloom launches Wholesale Nickel Program to support floriculture sustainability
- Be the source
- pH Helpers
- Society of American Florists accepting entries for 2025 Marketer of the Year Contest