
Thermostats are still the major heating/cooling system control device for many growers. Although accurate mechanical and electronic thermostats, controllers and computers are readily available, they have not been widely adapted in many smaller operations due to their cost and unfamiliarity to growers. Selecting the right thermostat and locating it to sense plant temperature can save considerable fuel and electricity.
Best location
I have seen thermostats located on end walls, attached to the heater or fan, above fin radiation, in direct line of heat from a furnace and in direct sunlight. If yours are in these locations, they should be moved. They will not provide accurate plant temperature sensing there.
Locating the sensor near the center of the greenhouse or crop area is best as it reduces the effect of heat loss through the glazing. Keep them away from operating equipment, dripping water or a dusty location. Use a chain to hang them so that they can be kept at plant level. Locate heating and ventilation equipment thermostats in the same area so they sense the same air.
Shielding is important
Thermostats and sensors should be shielded from direct sunlight as this can give false readings. A good installation is to place all thermostats inside a closed aspirated box that has been painted white. With a screen on one end and a small muffin fan on the other, air will be drawn through and all sensors will get the same temperature air. This technique is standard on most controller and computer control systems.
Clean your sensors
I have seen thermostats coated with a 1/4-inch-thick layer of dust. This will result in inaccurate readings. Use a can of compressed air to blow the dust off the sensor and the box. Purchase thermostats with a sealed box and use watertight electrical connections.

Loss of accuracy
Thermostats and sensors tend to lose accuracy over time. They should be checked at least once a year. I have had growers tell me that even new thermostats were inaccurate by as much as 10° F.
It is easy to check the accuracy of a thermostat. Start by checking the accuracy of a thermistor or thermocouple thermometer. These are inexpensive, fast-acting and have an easy readout. Insert the probe into an ice water bath. The reading should be 32° F.
After allowing the thermometer to reach room temperature, place it next to the thermostat sensor. Slowly move the dial until the heater turns on. The reading should be the same temperature as the thermometer reading. If not, determine the temperature difference and mark the thermostat accordingly. The next time the heating system is serviced, have the serviceperson recalibrate the thermostat.
Thermostat selection
The harsh greenhouse environment requires a good thermostat. Select one that has a hydraulic sensor activated by pressure from the expansion of a liquid or gas in a closed tube coil.
The movement of the switch between the On signal and the Off signal is called differential. This can vary from 2° F to 8° F. For example, if you have a setpoint of 60° F and a thermostat with a 5° F differential, the heater will start when the temperature reaches 60° F but doesn’t shut off until 65° F. Every degree above the setpoint increases heat loss from the greenhouse and heating cost by about 1.5%. It is important to select a thermostat with a +/- 1° F differential. The Dayton thermostat used by many growers has a differential of +/- 3° F.
The savings can be significant. For example, for a 30-foot by 100-foot greenhouse the savings between a 2° F differential and a 6° F differential thermostat can be as much as 500 gallons of fuel oil, 750 gallons of propane or 700 therms of natural gas over the fall to spring heating season. The payback is short.
Good controls that are maintained properly provide heating/cooling equipment with a means of operating at peak performance and efficiency. Now is the time to maintain, calibrate and replace the controls in your greenhouses.
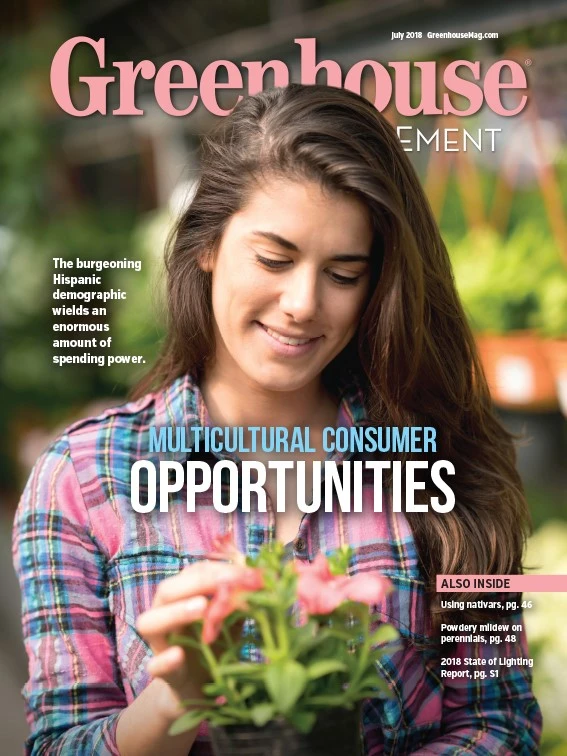
Explore the July 2018 Issue
Check out more from this issue and find your next story to read.
Latest from Greenhouse Management
- The Growth Industry Episode 3: Across the Pond with Neville Stein
- Trends: Proven Winners 2025 perennial survey shows strong demand
- Online registration opens for the 2025 Farwest Show
- Green Gear: Battery-powered backpack sprayer and a hoodie
- Sustainabloom launches Wholesale Nickel Program to support floriculture sustainability
- Be the source
- pH Helpers
- Society of American Florists accepting entries for 2025 Marketer of the Year Contest