

Filling containers is one of the large labor users in the production of plants. The typical hand-filling rate of 60 to 100 flats/person-hour is considered good. On the other hand, machines are available that will fill more than 1,000 flats/person-hour.
The advantage to choosing a machine over hand-filling is the uniformity of media in the container. There are no compacted areas. This results in more uniform watering and therefore more uniform plants.
Although a tray filler can be used as a standalone machine, they are more efficient if they are part of a production line. Tray fillers can include a soil feeder, seeder, transplanting machine or conveyor, watering tunnel and tagger. It is usually best if all equipment is purchased from the same manufacturer so the components match.

Basic components
What should you look for in a container-filling machine? The following are the basic components of most machines.
Soil bin — The bin should be able to handle the type of mix you are using without bridging or sticking. Bin capacities ranging from 6 cubic feet to 4 cubic yards are available. One yard will fill about 75 flats or 480 6-inch pots.
Conveyor for flats — A belt or chain conveyor is used to move the containers under the soil bin or flight conveyor. A variable-speed drive, either electric or hydraulic, will allow you to adjust the feed rate depending on the size of the container. Feed rates of five to 30 trays per minute for small machines and 20 to 60 for large machines are common. Pot rate will depend on size and whether they are individually fed or are placed in a template tray.
Soil feed — Most manufacturers use a rubber belt to carry trays. The amount of mix that is fed depends on the adjustment of the discharge gate. A few machines use a vibrating feeder. A speed adjustment on the belt helps to adjust the soil feed rate to the containers.
Soil wiper — When the soil is placed in the container it is usually pretty fluffy. Some compaction is needed to reduce the air space and ensure that when watered it doesn’t settle too much. For filling plug trays, a vibrator helps to settle the mix and make the substrate homogenous throughout the cavities. Most manufacturers use an adjustable wiper to remove excess mix.
Brush — After compaction the excess soil on the container is removed by a fixed or revolving brush. This is adjusted to clean the finished flat.
Soil return — The more expensive fillers have a conveyor that catches excess soil and returns it to the soil bin. This is a nice option, but if a machine is properly adjusted there should be very little excess soil.
Power source — The lower-cost machines are powered by several fractional horsepower gear motors. Some are variable-speed such as the belts, and others are constant-speed such as the soil return or brush. Manufacturers of larger container fillers have gone to using hydraulic motors. This allows variable-speed control, longer life and less maintenance. For convenience all of the controls should be located in one area, preferably in a dustproof box. Safety devices include a convenient shutoff switch and guards for moving parts.
The typical hand-filling rate of 60 to 100 flats/person-hour is considered good. However, machines can fill more than 1,000 flats/person-hour.
Accessories
Most manufacturers offer some accessories that increase the versatility of the filler and perform additional labor-saving steps. Options include:
Reciprocating punch — These come in types that can do a whole flat or types that do only one row of holes at a time. For plug trays a rotating cylinder with buttons may be used.
Counter — A counter is another time-saving option that keeps track of production. Both mechanical and electric eye units are available.
Automatic container destackers — These feed flats into the filler filler. Check to see what sizes and styles of container it will handle.
Continuous container filling and planting systems — Using these systems, fertilizer, pesticides and seed-covering material can be added with a feed device.
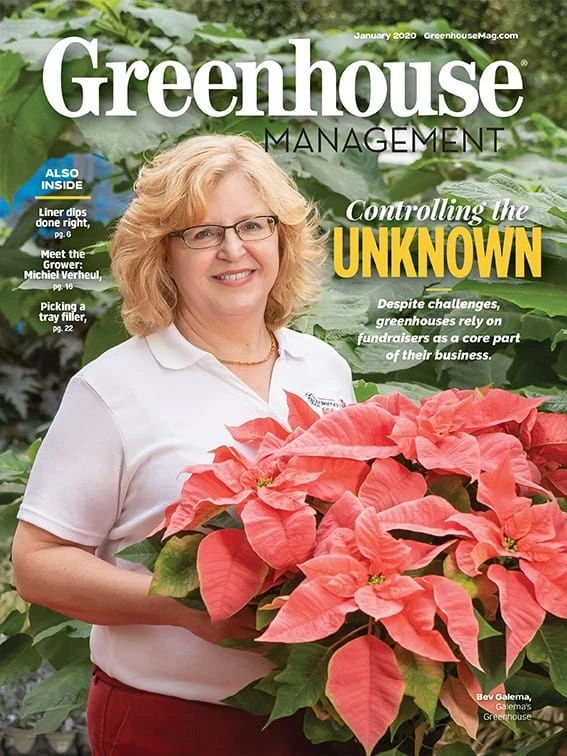
Explore the January 2020 Issue
Check out more from this issue and find your next story to read.
Latest from Greenhouse Management
- Flexible fungicides
- Super Charged Moon Juice from Moon Valley Nurseries now available nationally
- 2025 Proven Winners Horticulture Scholarship applications now open
- How to improve inventory and shipping management in the greenhouse
- Leading Women of Horticulture: Anna Ball, Ball Hort, and Terri McEnaney, Bailey Nurseries
- GM CEA HERB Part 2: A guide to increasing the sowing density of culinary herbs
- GM CEA HERB Part 1: Best practices for producing culinary herbs in controlled environments
- USDA fires experts on invasive pests, including Asian citrus psyllid, chilli thrips