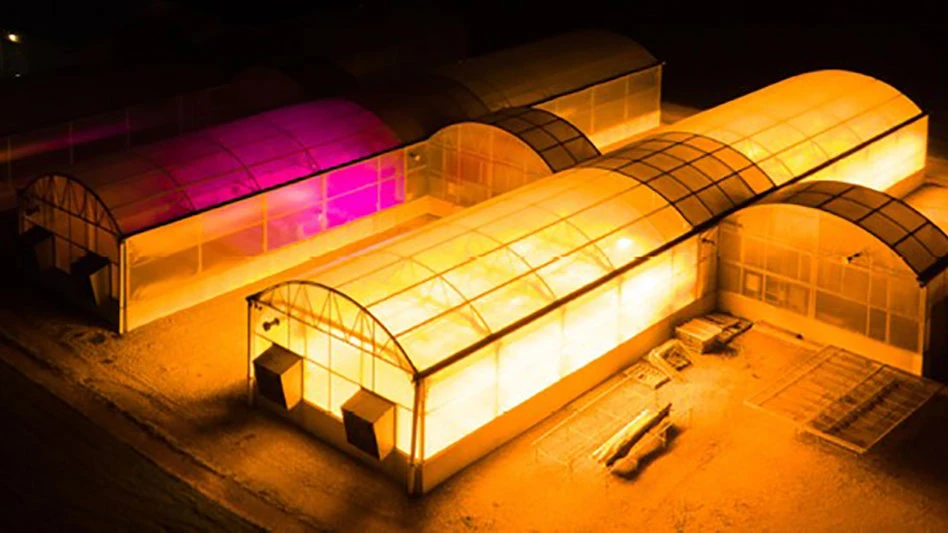

When it comes to upgrading your supplemental lighting system or planning for new greenhouse construction, it’s not just a matter of installation and then flip a switch. Make sure you are working with an expert who can create a comprehensive lighting plan designed for your needs, says Brandon Robinson, a technical services engineer at Hawthorne Gardening Company.
Step one
Prior to a lighting upgrade or new construction, you need to first outline your goals.
“Are you adding supplemental lighting to increase light levels and achieve more yield, or are you trying to extend the season so that you can maintain light levels that you currently get from the sun?” Robinson poses.
Once you’ve determined the “why,” you’ve got some homework to do. First call your power company to make sure your area has enough power available.
“Lighting loads are significant, so knowing how much power you have available to your facility is crucial,” Robinson explains. “We’ve actually seen this with some growers in Leamington, Ontario, which is a huge greenhouse capital. Growers there are fighting for power. Some of these greenhouses want to build out and put in supplemental lighting because they understand the benefits of it, but there’s only so much power available in that area.”
The light levels that you're trying to achieve also ultimately depend on the size of the project, which then reflects how much power you’ll need.
The lighting loads won’t be as high for an ornamental grower, but if you’re considering starting a cannabis crop, you’ll require more power, he adds.

Step two
Once you’ve determined the power condition at your facility, the next step is to reach out to a lighting manufacturer with an in-house design team that can provide a light plan.
“In the case of our in-house design team, we’ll walk you through everything we need to create the proper light plan,” he says.
The basic components of a light plan include:
- Greenhouse dimensions – if you have blueprints, provide them.
- Dimensions of each bay
- Dimensions of the plant canopy – what size is the plant when you bring it in and what size is it when you ship it out?
- Bench height
- Note any obstructions such as heating pipes, etc.
- Desired light levels
- Power capacity
Providing the plant canopy dimensions are important to uniformity.
“At Hawthorne GC, we try to plan for that slight variation in light levels from young plant to finished plant since there will be some differences in uniformity. We want to give you the best of both worlds for starting and finishing the crop,” he explains.And if you have any light readings from a weather station or data from a par sensor or light meter, that historical data is excellent information to provide the company creating your light plan.
“There are websites available where you put in the longitude latitude of a location and it will give you the average expected sun there. But if you have historical data that you can provide to a lighting team, then they can see the actual amount of sun you get in your area. And they can better tailor the light design to that data and not over-design. That historical lighting data can make your lighting plan a lot more tuned in to your actual needs,” he adds.
Changing over from HPS to LED lighting is the most common upgrade.
If you discover there’s a power issue at your facility but you need more light, it’s important to understand that LEDs use less power to achieve the same amount of light as the HPS fixtures, Robinson explains. Perhaps your light levels are sufficient, but you want to save money on electricity costs. An upgrade to LEDs can drop your energy use by 20-30%, depending on the fixture, he adds.
When Hawthorne creates a light plan, they also calculate the ROI for your investment.
Another consideration when researching LEDs is understanding the light spectrum, Robinson explains.
“We have a team that can talk about how different plant types respond to light spectrum and explain how, for instance, that heavy orange that comes out of an HPS fixture vs. the spectrum from an LED can have a variety of morphological differences on the plant,” he says. “There are a ton of research papers out there about different plant types and what different wavelengths can do to the plant. It comes back why we always suggest getting a light plan.”

Step three
Now that you’ve got a light plan, it’s time to look for a contractor to handle installation.
“A larger grower may go through a greenhouse building contractor or an architect,” he says. “If that’s the case, Hawthorne has made all of our IES files public — files needed to create lighting simulations, allowing designers outside the Hawthorne tech services team to create light layouts. We are leading the way in making our products more accessible to the grower.”
Something to discuss with your installer prior to work beginning: are they planning to follow the trusses already in place inside the greenhouse?
“Of course, you want the most uniformity in your crop, which affects the placement of the lights. So you have to look at both options of using the existing trusses or building some sort of subframe,” he says. “If you can use the infrastructure that's already there, great. That's a massive cost reduction.
“One thing to ask yourself or discuss with your installer is if the ideal light placement is going to cost X amount more and it only gets me, say 5% better uniformity, that’s not worth the cost. Instead, take a little bit of a hit to uniformity to save a ton of money on installation.”
Considerations and misconceptions
When changing out fixtures from an HPS to an LED, don’t assume everything is going to be the same. For instance, one HPS fixture has a fair amount of variants because of the reflectors. And when you change to LEDs, “you’re changing the total photon output and distribution of light,” Robinson says. “HPS may throw light really wide, but LEDs can have a more narrow light spread so the uniformity across the crop changes.”
A grower will need to understand the key differences between their old lights and their new selections in order to adjust.
For LED fixtures in a greenhouse, Robinson suggests the compact, top-light style.
Does it make sense for growers to consider HPS lighting? Robinson says yes and no.
“There is still a place for HPS, but that is getting smaller and smaller all the time. For some, it’s a budget consideration. LEDs will have more upfront costs, but they have come down in price a great deal. But if you look at the lifecycle of the fixtures, the LED will ultimately be cheaper in the long run. And as the world starts to look more and more at energy efficiencies, HPS might eventually be regulated out of the market completely,” he says. “If you live in an area that will mandate growers into using LEDs, it’s better to be already using them and past the learning curve before being forced into it.”
Some growers rely on the radiant heat that’s emitted from the HPS fixtures.
“I get that, because LEDs take much of that heat and it put it in the heat sink and throw it out. That’s a consideration. Maybe when they take out that less-efficient light, they lose some heating benefits. Now maybe the grower has to use a heater, maybe a gas heater, and that gas is more expensive than the electricity they were just paying for with the lighting. But there are ways to more efficiently heat your greenhouse, too. If you’re looking at a new build, I don't think there's any reason to do HPS.”
HPS lamps require more maintenance than LED lights.
“With LEDs, there’s very little maintenance. They’re pretty well a set-and-forget piece of equipment,” Robinson explains. “Some specific fixtures have a polycarbonate lens that you may need to wipe down every once in a while just in case any material has built up on the optic. You can also wipe down the heat sink for the same reason. That will help maintain the efficiency of the LED.”
And LEDs are designed to run for tens of thousands of hours before they completely degrade. “For example, our 1930e LED fixture has a degradation rate of Q90, which means the bulb reaches 90% of its operating efficiency at 50,000 hours,” he adds.
LEDs have come down in price while energy prices are on the rise.
“We’re at the point where LEDs are at a pretty good price right now and in many areas rebates may be available. And when you work with Hawthorne, we partner with a company that will help you find those rebates,” Robinson says. “But as more time goes by and more states start to mandate changes to LED, those rebates will start to go away. Don’t miss out. Once it’s mandated by the state, the power company is less likely to give out an incentive.”
The bottom line: upgrade to LEDs “if it makes sense financially and if it’s going to benefit your facility, your plants and your infrastructure. If you save energy, you save money. If you’ve got better light on your crop, you’re likely to get better yield, which makes you more money,” Robinson says.
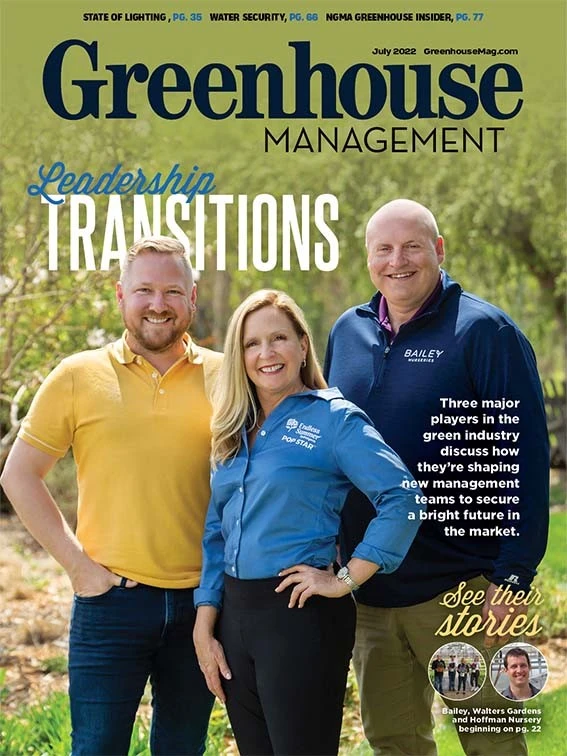
Explore the July 2022 Issue
Check out more from this issue and find your next story to read.
Latest from Greenhouse Management
- This month's Greenhouse Management magazine is about native plants and sustainability
- The HC Companies, Classic Home & Garden merge as Growscape
- Terra Nova releases new echinacea variety, 'Fringe Festival'
- Eason Horticultural Resources will now officially be known as EHR
- BioWorks receives EPA approval for new biological insecticide for thrips, aphids, whiteflies
- ScottsMiracle-Gro transfers cannabis subsidiary to focus on core lawn and garden business
- Should we start calling natives 'eco-beneficial plants'?
- Ellen Mackenbach-Lakeman appointed new CEO of Dümmen Orange