Great Lakes Greenhouses produces a large quantity of Wave petunias for larger growers — mostly 6-inch pots, six plants to a pack, with minimal transplanting requirements. But recently, they’ve grown their pack plant business in spring and fall, which put a seasonal labor strain on production.
“When we started getting 36 to 60 plants per pack, we had to get so many people on the planting line to produce the weekly numbers we needed to,” says owner Mike Klooster. “The issue was being able to get the work done in the time frame that we have to do it in, and the limitations we have with the labor that’s available.”
Klooster had seen TTA USA’s PackPlanter in action at his brother’s greenhouse (Klooster Greenhouses, also located in Kalamazoo), so this spring, when Great Lakes hit the production volume to justify an automated transplanter, he got one, too.
“We needed to have a couple hundred thousand units to run through the machine on an annual basis in order to make it pay,” Klooster says. “We run it for two to three months in the spring, and again in the fall for a couple of months, and it has benefitted us in ways we didn’t think it would.”
Klooster expected the labor savings: The PackPlanter transplants 400 to 700 flats or packs per hour, with support from about eight people. Though the manual line could transplant 400 to 500 per hour, it required 20 people from start to finish. With automation, Great Lakes didn’t have to hire any temps this spring.
But that’s not all.
“One of the hidden benefits that we didn’t realize until we ran it for a season is that we had fewer issues growing crops after they were transplanted,” he says. “Quality actually improved with the PackPlanter, because it orients the root cube correctly. Our percentage loss of crops was significantly reduced, and we were really happy to see that.”
Because of the combined labor savings and precision, even smaller greenhouses can benefit from the PackPlanter. Stelz Nursery, with just under 65,000 square feet of covered growing space, started using TTA’s PackPlanter in the spring of 2015.
“Previous transplanting machines were too expensive for a small business, and they weren’t as precise in transplanting,” says Elizabeth Stelz, secretary-treasurer and general manager. “The cost of the [PackPlanter] per month was less than two full-time human transplanters, and that’s the main reason we got it: Labor is increasingly difficult to find. We only use American workers, and without bringing in H2B employees, we could not produce the number of flats that we needed with the labor we were getting.”
Stelz uses the PackPlanter to transplant up to 90 percent of its product line grown in 288 or 324 plug trays. On its slowest setting, the PackPlanter transplants more than 200 flats per hour — compared to 50 or 60 flats per hour with human transplanters. Employees who previously transplanted now help with plant maintenance and delivery, which streamlines operations.
“It virtually eliminated the unreliable human element of absences and slack performance, with great efficiency and accuracy,” Stelz says. “The savings are evident.”
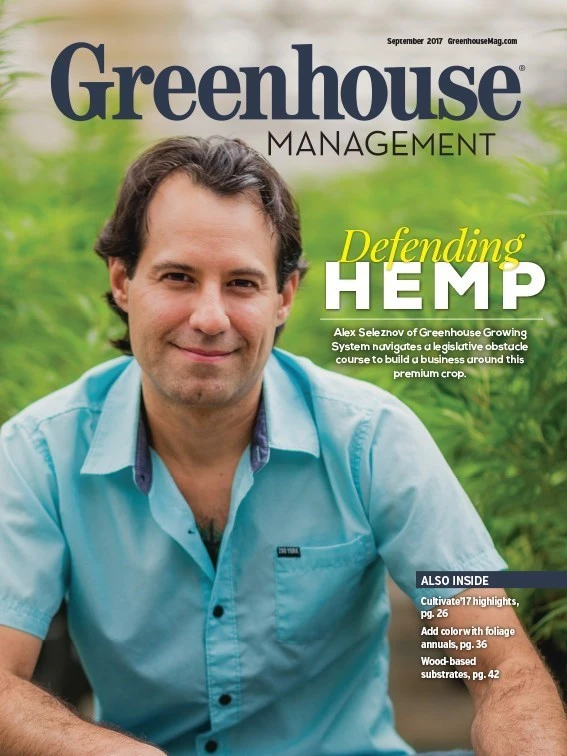
Explore the September 2017 Issue
Check out more from this issue and find your next story to read.
Latest from Greenhouse Management
- North Carolina Nursery & Landscape Association announces new executive vice president
- Plant Development Services, Inc. unveils plant varieties debuting in 2025
- Promo kit available to celebrate first National Wave Day on May 3
- Applications now open for American Floral Endowment graduate scholarships
- Endless Summer Hydrangeas celebrates 20 years with community plantings
- Invest in silver
- Garden Center magazine announces dates for 2025 Garden Center Conference & Expo
- USDA launches $2 billion in aid for floriculture growers