
Chipped, shredded, or fiberized, wood was once thought to be a possible alternative to peat moss, and is now a reality. Commercially available wood-based substrates are becoming more commonly trialed among greenhouse growers or implemented in greenhouse production (Fig. 1). While there are a handful of commercialized wood-based substrates available to greenhouse growers, smaller localized substrate producers and growers have begun formulating their own mixes with wood materials. Whether you purchase a pre-formulated wood-based substrate or incorporate wood materials as components or extend your peat supply with a pre-formulated wood-based substrate, success and challenges with the substrate will vary.
Consistency
Considering making the switch or trialing a wood-based substrate? Before making the plunge, it’s important to keep in mind that not all wood-based substrates or components are produced the same. Research and development of wood components as a replacement or alternative to "traditional" greenhouse substrates and components has been the forefront of Dr. Brian Jackson and Dr. William Fonteno’s research at North Carolina State University, which you can read at bit.ly/2hKRLKp
Much of their research is to understand wood as a substrate component, how to consistently and repeatedly produce wood materials for substrates, and use of wood materials in greenhouse plant production. From the many research experiments and trials, there seems to be an overall theme for wood-based substrates — consistency. Consistency of wood materials or components, type of wood, availability, and the production method in which the wood material will be used are all important points to consider. These considerations should be addressed before making the switch to pre- or self-formulated wood-based substrates.
Wood materials
Wood materials that are used to formulate a wood-based substrate vary in physical and chemical properties. For instance, wood materials to be used as substrates or components can be produced from various hardwood and softwood trees and may be chipped (Fig. 2A), shredded (Fig. 2B), or fibrous/ground (Fig. 2C). Physical properties such as the particle size and shape of the wood materials will directly influence the substrate and how it performs during production. For instance, chipped wood such as those I reported on at bit.ly/2i3LSb9, is blockular and can be used as an alternative to perlite in greenhouse substrates, while a fibrous wood material mimics many properties of fluffed or expanded peat moss. This fibrous wood material is one of the most popular materials being commercially produced as a peat moss alternative or replacement. To produce the various physical properties of either chips or fluffy fibers is no easy task, but a science that Drs. Jackson and Fonteno are becoming closer to understanding during processing of raw wood. In addition, chemical properties such as pH, electrical conductivity (EC), phytotoxicity, and the efficacy of applied plant growth regulator drenches of wood materials are of interest and have been previous explored for pine wood chips that I reported on. Additionally, these properties may vary among tree species, time of the year trees were harvested, and age of the wood materials (fresh vs. aged).

Commercially available wood-based substrates
There are a few commercial substrate producers developing and marketing wood-based substrates. Overall, these substrates vary from shredded and pulverized wood to fibrous peat-like doppelgänger materials. Interestingly these products are handled similarly to peat and coir, meaning they are also compressed for ease of shipping and storage, but require fluffing prior to use. While there may not be an answer of which producers’ wood-based substrate is better than another, it is recommended that growers perform in-house trials of various wood materials and mixes to determine which works best for your greenhouse operation, equipment and production method.
Challenges
While visiting greenhouse growers around the U.S. and in Europe, I have seen some of the challenges of wood-based substrates. The most common challenge is the substrate mixing equipment and flat or container fillers. The most common problem is that free-flowing wood fiber high in moisture content can build-up on the side of mixing equipment, and thus, causing clogs and producing clusters of un-fluffed balls of fibrous wood. However, I have also seen this similar challenge with peat moss and coir that was either shredded or chipped/chunked respectively. Regardless, each substrate material has its own production challenges but one thing is certain, wood-based substrates will change how the industry thinks about growing media.
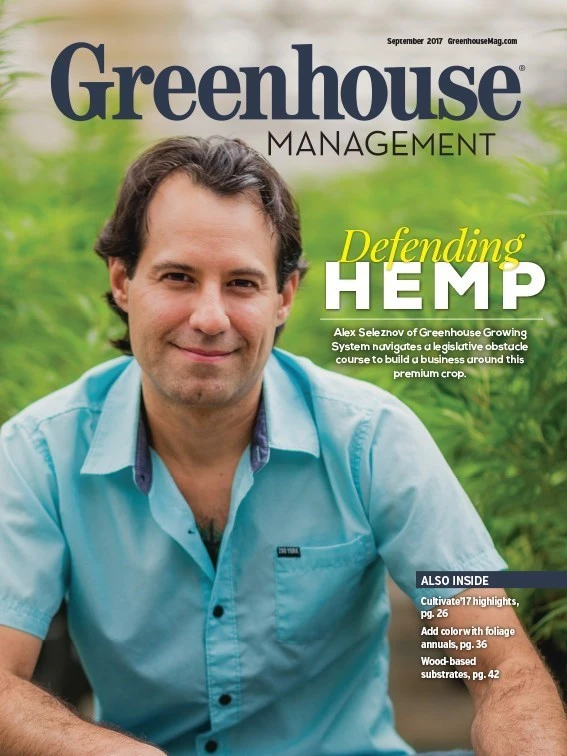
Explore the September 2017 Issue
Check out more from this issue and find your next story to read.
Latest from Greenhouse Management
- Flexible fungicides
- Super Charged Moon Juice from Moon Valley Nurseries now available nationally
- 2025 Proven Winners Horticulture Scholarship applications now open
- How to improve inventory and shipping management in the greenhouse
- Leading Women of Horticulture: Anna Ball, Ball Hort, and Terri McEnaney, Bailey Nurseries
- GM CEA HERB Part 2: A guide to increasing the sowing density of culinary herbs
- GM CEA HERB Part 1: Best practices for producing culinary herbs in controlled environments
- USDA fires experts on invasive pests, including Asian citrus psyllid, chilli thrips