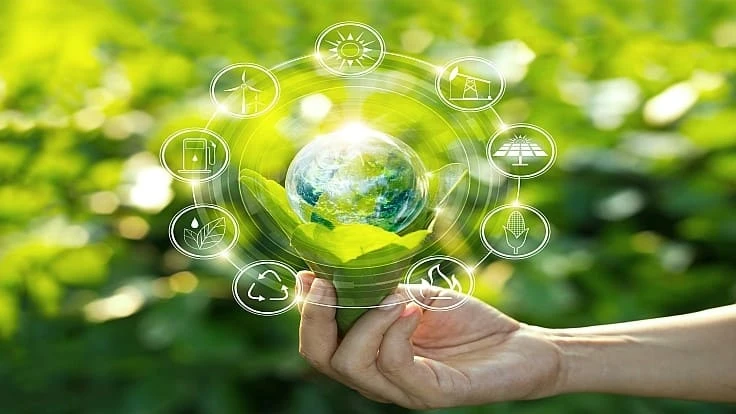
Photo Credit Adobe Stock
There is a sea of change coming — heck, it’s already here for much of the country — and it’s 100% going to affect your bottom line as a CEA grower.
We’re talking, of course, about rising energy costs.
This is a touchy subject that was covered adeptly by Michigan State University horticulture professor and researcher Dr. Erik Runkle at AmericanHort’s inaugural Finished Plant Conference. The event took place in Grand Rapids in mid-October, and it featured a solid program of production-focused content perfectly suited for serious commercial greenhouse grower leads and section growers.
“Energy prices have been (relatively) cheap for some time,” Runkle told attendees. “Now, we’re seeing pricing increases almost across the board — especially when it comes to heating costs.”
Those increases are being driven by supply chain difficulties, inflation and just a generally higher level of demand (since more people are spending more time at home), but luckily, it’s still not as bad as what our friends who grow in greenhouses across the pond are dealing with. At least … not yet.
“Natural gas prices are going up quite a bit lately, but it’s still not as bad as it was during the economic crash in 2008, or the prices they’re paying over in Europe,” Runkle explained. “We’re fortunate to have relatively cheap energy here in the U.S., knock on wood.”
Runkle and his team of researchers in East Lansing and around the Mitten State are responding by focusing a portion of their research on ways that growers can produce high quality crops in shorter crop times with the least amount of energy possible.
During his presentation, Dr. Runkle shared these four “no-brainer tips” for growers looking to uncover greenhouse energy savings this coming season as energy prices spike:
- Use infrared anti-condensate polycarbonate film (where possible) as a covering. Runkle advised that spending a little more upfront on coverings featuring IR reflecting material with anti-condensate properties can dramatically lower your fuel consumption when you’re heating the greenhouse. And he said the return on investment for double poly is usually realized in less than a full calendar year.
- Reduce air leaks or add insulation. Runkle recommended growers regularly inspect structures for gaps or leaks, and seal them as quickly as possible. When using poly coverings, use the outside air to inflate the two layers between the double poly, because he says that if you use air from inside the greenhouse, you can have moisture trapped between the layers, which is not ideal.
- Utilize and maintain horizontal air flow fans. This one seems counterintuitive, as generally speaking, more fans running should equal higher energy usage, but Runkle stressed it for a very good reason: poor air uniformity results in non-uniform growth and development, and it increases the temperature gradient (i.e. the range of temperatures in different areas) inside your structure as well, which is not good. “If you don’t have good circulation, you can get air stratifications and layers of various temperature air throughout the house, and subsequently, your heating/cooling/ventilation equipment all has to work harder, which in turn means more energy consumption,” he explained. Runkle recommended staging fans throughout the greenhouse, above the plants, and the fans should be rated to move 3 cubic ft. of air per minute per square foot of space.
- Use of energy and/or shade curtains. This one includes an often-expensive upfront capital investment to purchase the curtains/screens, but Runkle said that payback is typically quick. Greenhouse growers that MSU has surveyed around Michigan have reported energy savings around 30% on average by adding a well-maintained energy curtain. He noted that 30% energy consumption decrease roughly equals a payback period of three years until the equipment is paid for, but there are USDA grants and utility rebates for producers that implement the screens, depending on what state you grow in.
Get curated news on YOUR industry.
Enter your email to receive our newsletters.
Latest from Greenhouse Management
- CEA Alliance celebrates bipartisan introduction of Supporting Innovation in Agriculture Act
- Dümmen Orange North America celebrating 25th anniversary in 2025
- Illinois Landscape Contractors Association changes name to Landscape Illinois
- 2025 Proven Winners Horticulture Scholarship applications now open
- ICL’s Gemini Granular herbicide now registered for use in California
- Eurazeo Planetary Boundaries Fund acquires Bioline AgroSciences
- Spring Meadow Nursery's Freedom Shelley finds joy in plants
- Leading Women of Horticulture: Dana Massey, Plantworks Nursery