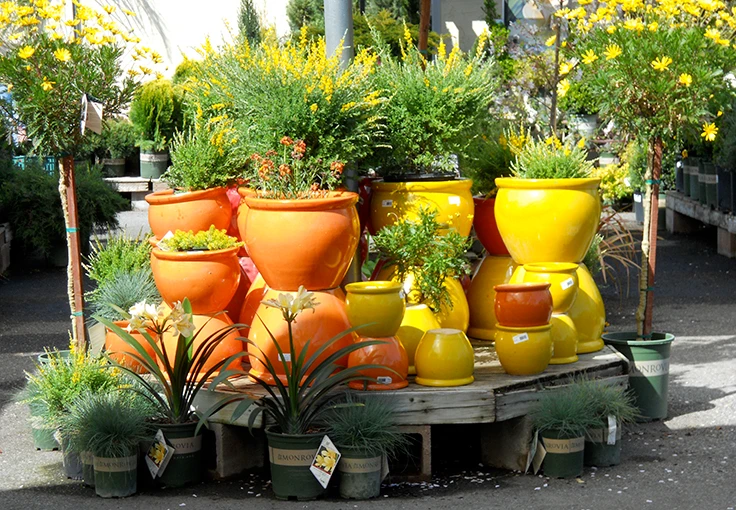
The same amount of care and concern should go into creating a solid safety program as was taken to craft your business plan, mission statement and financial strategy. A safe workplace helps reduce accidents and improves employee satisfaction, which ultimately saves the company money.
When it comes to developing a safety program, companies should include some key components, says Jill Hoffmann, senior loss control consultant at Hortica®, a brand of the Sentry Insurance Group.
Management commitment and employee involvement. Develop a policy stating the importance of safety and health at your workplace, top management’s commitment to safety, responsibility assignments regarding safety and health within the organization, how managers/supervisors/employees will be held accountable for enforcing and following safety rules, and an annual review of the program’s goals and objectives.
Worksite analysis. Conduct regular site inspections to identify and correct hazardous conditions, outline steps in reporting hazards so they can be addressed, perform accident and near-miss investigations, and analyze trending claims to develop action plans.
A hazard is anything that has the potential to cause harm/injury to an employee, customer, or visitor, as well as property damage. This includes safety hazards (spills, inadequate machine guarding, electrical hazards, equipment/machinery safety and maintenance, etc.), biological hazard (blood-borne pathogens, insect bites, mold, etc.), physical/environmental hazards (heat/cold stress, noise and sun exposure, etc.), ergonomic hazards (repetitive motion, awkward movements/posture, frequent lifting, etc.), chemical hazards (unlabeled chemical containers, vapors from chemicals, carbon monoxide, etc.), and workplace organizational hazards (sexual harassment, workplace violence, work demands, etc.).
Hoffmann recommends performing workplace inspections at least once a month. The inspections should include all areas of the facility and grounds, housekeeping, electricity, lighting, heating and ventilation, machinery, personnel, chemicals/pesticides, fire prevention, maintenance, PPE, transportation, first aid program, and evacuation plan. Try to alternate employees to assist with inspections because it helps prevent hazards from being overlooked.
Hazard prevention and control. Ensure hazardous or potentially hazardous conditions are identified and corrected. Once hazards are identified, prioritize them and quickly address and correct situations that pose an immediate danger to life or health and/or pose a high risk of severe damage/loss to property.
Consider listing hazards on an Excel spreadsheet for easy tracking and so the list can be altered, moving the most critical needs to the top of the list.
Safety and health training and education. Educate employees on potential hazards to prevent injury/illness, and train supervisors/managers so their responsibilities are understood.
While there is no federal OSHA requirement regarding the frequency of general safety training, some topics do have an OSHA-specific timeframe for refresher training, such as fire extinguisher training and forklift operator training. Some state OSHA plans have more stringent requirements than the federal OSHA requirements. It is important though to complete regular in-house safety training to maintain your safety culture and continue to improve safety. Hoffmann suggests holding regular safety meetings once a month at a minimum.
Latest from Greenhouse Management
- 2025 Proven Winners Horticulture Scholarship applications now open
- How to improve inventory and shipping management in the greenhouse
- Leading Women of Horticulture: Anna Ball, Ball Hort, and Terri McEnaney, Bailey Nurseries
- GM CEA HERB Part 2: A guide to increasing the sowing density of culinary herbs
- GM CEA HERB Part 1: Best practices for producing culinary herbs in controlled environments
- USDA fires experts on invasive pests, including Asian citrus psyllid, chilli thrips
- CEA Alliance celebrates bipartisan introduction of Supporting Innovation in Agriculture Act
- Dümmen Orange North America celebrating 25th anniversary in 2025