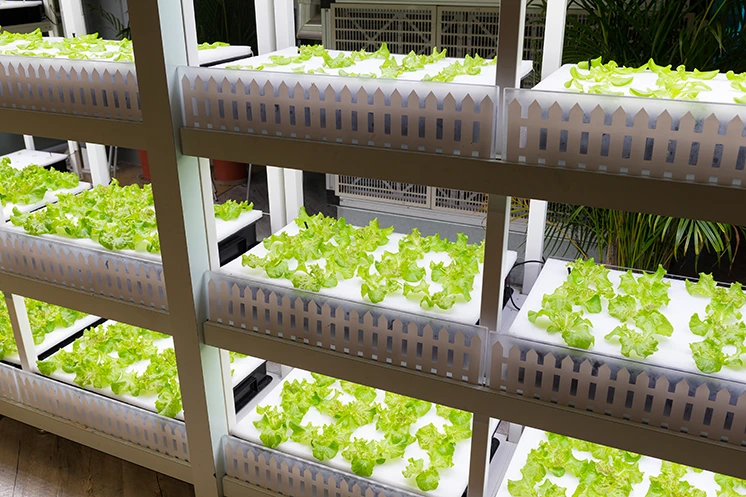
The world is undergoing a revolution in horticultural lighting that will have wide-ranging implications in terms of how and where we grow, and what crops we consume. The move from high-intensity discharge (HID) lighting to LEDs is slashing electric bills for indoor farmers. Alongside cost, the reliability and longevity have both improved, reducing maintenance requirements.
The “instant on-and-off” aspect of LEDs makes them easily integrated into automated growing cycles to maximize plant growth. And with wavelengths optimized for different crops, power usage can be reduced further. The lower heat output of LEDs means plants can be grown closer to light sources, allowing for better use of space.
Analysts LED Inside predicts the market will reach USD $500m by 2017, while WinterGreen Research sees it reaching $1.8 billion by 2021.
LED technology is likely to transform the horticultural industry
The argument for LED grow lighting is increasingly one of economy. The reduced running costs of LEDs has moved the market from high-value crops like cannabis, to lower-value fruit and vegetables, which is having a transformative effect on the industry.
LEDs allow affordable cultivation in previously inaccessible places such as tower blocks in city centres, extreme climates or areas lacking natural light such as the Arctic Circle in winter. Innovations like vertical farming, where plants are tightly stacked on floor to ceiling shelving with closely positioned LED lights, make enormous crop yields from a small footprint possible. Such techniques improve the consistency and standardization of crops while reducing pesticide use. And locating farms close to consumers cuts transport and storage costs.
The societal implications are enormous. In enabling the affordable growth of a diverse range of crops, LED technology has the potential to improve worldwide nutrition, as well as to offset food inflation as populations increase. By enabling crops to be grown close to consumers, LED technology could offset ecological and ethical issues associated with the over-farming of high-value crops (such as avocados and quinoa) within highly localized regions.
\hermal management is a critical factor in the further evolution of LED grow lights
However, LEDs do have one issue: thermal management.
The type of LEDs generally used in horticultural lighting are high-brightness LEDs (HB LEDs), between 1–5W. Although massively more thermally efficient than HIDs, most HB LEDs are still only around 40 percent efficient, so 60 percent of the energy comes out as heat rather than light. Horticultural LED modules often have hundreds of HB LEDs mounted onto a printed circuit board (PCB), creating a considerable thermal challenge. If heat isn’t removed effectively it can have a negative impact on the LEDs, reducing lifetime and light quality and ultimately leading to the LED’s failure, and the plants themselves.Another factor to improve thermal management is growers’ desire to place plants closer to the light source without heat affecting the crop, thus allowing for tighter spacing and greater economies of scale.
There are two fundamental types of thermal management — active and passive. Active thermal management uses fans and pumps to push air or liquid through the LED module. Heat is conducted into this medium (air or water) and drawn away from the LEDs where it is radiated out into the atmosphere or used to warm soil. Passive thermal management uses materials to conduct the heat away. A heatsink is a good example.
Most designers are familiar with active cooling systems. However, heat must be removed at the level of the LED chip itself. If heat is not effectively conducted away from the LED chip, the whole system will fail.
How LED heat extraction works (at the chip and board level)
An LED module will, depending on the device, generally feature either “packaged” or bare HB LED dies mounted on a PCB. To keep this simple, let’s assume the use of packaged LEDs.
A packaged HB LED cannot radiate heat directly into the air due to the surrounding encapsulant. Heat must be conducted through the bottom of the LED, - usually via a ceramic mount that is part of the HB LED ”package” – through the PCB and then out to the thermal management system.
Traditional PCBs, such as FR4, are not sufficiently thermally conductive for HB LEDs. Instead, HB LEDs are mounted onto metal-clad PCBs (MCPCBs), a PCB that incorporates a metal heat spreader. Critically, this MCPCB must also feature a dielectric (electrically isolating) layer that sits between the metal board and the circuit layer to prevent the LED shorting. This dielectric layer must be sufficiently thermally conductive to conduct heat effectively to the metal layer beneath it.
Traditionally, MCPCBs use a layer of epoxy resin between the metal base and the copper circuit as the dielectric. As resins are poor thermal conductors, the epoxy is usually laced with grains of ceramic to improve its performance. However, ceramic-loaded epoxy resin cannot achieve really good thermal conductivity because individual ceramic grains must be separated from each other by epoxy to hold the material together. As the need to remove heat increases, existing MCPCB solutions are unable to meet the challenge.
A new approach is required — one that enables MCPCBs to reach a significantly higher level of thermal conductivity.
Nanoceramics — a new approach to MCPCBs
A new approach to MCPCBs has been developed that delivers thermal performance suited to the demanding needs of horticultural lighting. This approach uses a patented electro-chemical oxidation process to convert the surface of aluminium into a nano-grain alumina (nanoceramic) dielectric layer.
The thinness of this alumina layer (10–30 microns) is critical as it creates an extremely short, uninterrupted thermal path which the heat can move quickly. This gives nanoceramic a composite thermal performance of 115 W/mK. This is much higher than anything else available.
This performance enables horticultural grow light designers to push the limits of lumen density, squeezing more light out of smaller modules. Indoor farms can be built to a higher density helping to achieve higher yields on the same footprint, ultimately driving the economies of scale that are the critical factor for this new wave of farming to fulfil its potential.
John Cafferkey is Marketing Manager at Cambridge Nanotherm, an innovative company employing nanotech for the thermal management of LEDs headquartered in Haverhill just outside of Cambridge. John is responsible for developing and communicating Cambridge Nanotherm’s proposition to global LED manufacturers and designers.
Photos provided by Cambridge Nanotherm
Latest from Greenhouse Management
- 2025 Proven Winners Horticulture Scholarship applications now open
- How to improve inventory and shipping management in the greenhouse
- Leading Women of Horticulture: Anna Ball, Ball Hort, and Terri McEnaney, Bailey Nurseries
- GM CEA HERB Part 2: A guide to increasing the sowing density of culinary herbs
- GM CEA HERB Part 1: Best practices for producing culinary herbs in controlled environments
- USDA fires experts on invasive pests, including Asian citrus psyllid, chilli thrips
- CEA Alliance celebrates bipartisan introduction of Supporting Innovation in Agriculture Act
- Dümmen Orange North America celebrating 25th anniversary in 2025