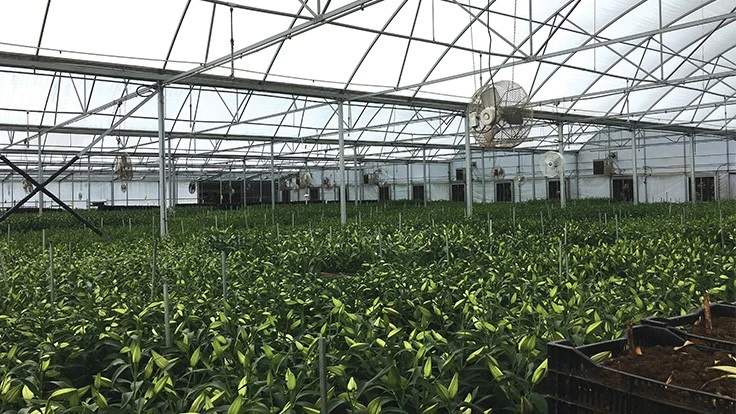

Michael Turner was living in Boston, studying political science as a graduate student, when he took a summer job working at a nursery in Lexington, Massachusetts. The job changed his entire career path.
“I fell in love with greenhouses and growing,” he says. “And I hated graduate school.”
Soon after, Turner moved back to his native North Carolina and started a part-time cut flower business while working full-time as a produce buyer for Whole Foods and other grocery chains. After a few years, he was able to commit to flower growing full-time and opened Sarah & Michael’s Farm, where he grows lilies. The business has been located at the same site in Durham, North Carolina since 1997. Now, his business operates year-round and sells to customers such as Whole Foods.
A key part of Turner’s business is his use — and reuse — of a coconut coir growing media; he recycles it for multiple production cycles. The idea to use coir, and recycle it, came from a grower back near where he took his first growing job. In 2006, he visited a lily grower named Fred Greene at Stow Greenhouses in Stow, Massachusetts. Greene used and recycled coconut coir and showed Turner the ropes. Soon after, he switched Sarah & Michael’s Farm's production to the material and now only grows in coconut coir.
“We had gone through every conceivable mix of growing media,” he says.
The advantages of coconut coir
Turner plants lilies in the crates that the bulbs are shipped in — a common Dutch growing method, he says — in the coconut coir. Each greenhouse is full from end-to-end with just enough room left to properly access and monitor each lily as it grows.
Turner, who sources his coconut coir from Sri Lanka through a Canadian importer, says the biggest reason coconut coir works so well is because it is a “superior rooting media.”
“The lilies just thrive in it,” he says. “Growing lilies is about growing really good roots, and lilies root really well in coir. And it matters that I am growing cut flowers and not something else because coir itself is a fairly light media. If it were a potted plant, I would have to worry about it tipping over.”
Additionally, Turner says coconut coir, unlike other growing medias he’s used, holds up well when steamed, cooled off and then reused. When he begins the recycling process, the coir fibers hold up well to the heat. To recycle it, a small percentage (the exact percentage depends on the week) of fresh coir is added to the used coir to keep the structure intact.
“It holds up much better than peat moss, for instance,” Turner says.
He adds that it helps that he has a consistent supply of coir; it hasn’t caused the issues he’s seen other lily growers face. For instance, Turner says high salt and potassium levels are a possible issue in coir, and if one or both is prevalent, it will negatively impact plant growth.
“That’s a natural property of the coir,” he says. “A good supplier will take care of those issues.”

Cost benefits
Turner says that importing coir from Sri Lanka a few times a year is “very expensive,” and it’s the main reason why he recycles his instead of using it and getting rid of it. Each year, he buys three containers for a total cost of around $35,000.
According to Turner, steaming the material also allows his business to avoid using any pesticides in the greenhouse because it preventively rids the coir of pathogens. Additionally, because of year-round aphid pressure in North Carolina, the coir cannot be used more than once before it is steamed. Other lily growers in the Netherlands and in Canada who he’s talked to use their coir twice before either recycling it or pitching it.
“If we weren’t recycling, instead of ordering three containers a year, we would be ordering four times that many containers at least,” he says. Right now, coir is Turner’s sixth-highest operational cost; it would likely be No. 1 or No. 2 without recycling.
Originally, Turner was steaming the coir in the crates they were grown in, but found that it caused the crates to break down and be unusable. In 2012, he switched to using a system where the coir is transferred into a bunker away from the greenhouse. There, it sits on top of piping that pushes steam up through the coir, refreshing it to be used again. The initial cost for the piping was high in the short term, but Turner feels it’s made the process more sustainable for his business.
“We know what’s in our soil,” Turner says. “We’ve taken out that wild card. When you buy soil, you hope you have a reputable supply. But by keeping it in-house so to speak, we feel like we have a lot better control over it. And the lilies love it.”
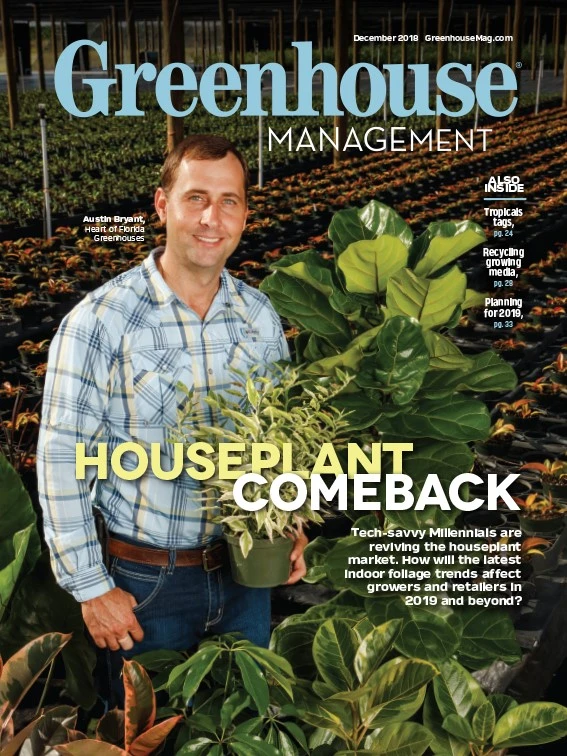
Explore the December 2018 Issue
Check out more from this issue and find your next story to read.
Latest from Greenhouse Management
- GIE Media Horticulture Group wins five regional 2025 Azbee Awards of Excellence
- Terra Nova Nurseries introduces rust-free and disease-resistant heucherella
- John T. Nickel, founder of Greenleaf Nursery Co., passes away at 89
- Three tours offered at 2025 Farwest Show
- Garden Media Group announces sixth annual Women in Horticulture Week
- Star Roses and Plants announces National Knock Out Rose Day
- The Growth Industry Episode 4: How federal budget cuts are affecting horticulture nonprofits
- Green Gear: Greenhouse tech for predicting weather and nutrient analysis