
If you ask the general public what they think of if you mention automation, they may first picture the machinery in big automotive manufacturing or food processing plants. And that’s with good reason — much research has gone into developing large-scale plants into fast, efficient systems that churn out the maximum number of products possible. However, the North American horticulture industry has shown growing interest in automating processes as the available skilled labor pool has shrunk and energy needs have changed, among other reasons.
Vineland Research and Innovation Centre’s researchers in Ontario have worked on many robotics and automation projects, from mushroom harvesting machines that can detect ripeness, to automated tulip planting technology to cucumber packaging machines. Dr. David Gholami, Research Scientist and Expert Systems Specialist at Vineland, worked in the industrial automation field before moving into horticulture. Greenhouse Management spent some time chatting with Gholami to get his perspective on automation in the horticulture industry and insights into his current research projects.
Greenhouse Management: How do industrial and horticultural automation differ in terms of development?
David Gholami: That’s actually an interesting question. In industrial settings, say automotive or oil and gas, the automation systems are far more advanced than [we have] now in agriculture or horticulture per se. There are different techniques, different machinery that we use to increase efficiency, to increase performance … When I came here to agriculture, I noticed there are applications [from industrial] automation that we could transfer. There are challenges involved, but we can still transfer them to horticulture ... and hopefully get the same or a similar performance and efficiency as we get in other industries.
GM: What automation and robotics projects are you working on now?
DG: Currently I’m leading two projects. One is smart irrigation of greenhouses, and the other one is disease detection of greenhouses. [Editor’s note: To read more about Gholami’s high-tech disease detection research, turn to page 42.] They are kind of related, and what makes them different than in any other industry is we are dealing with plants. They’re living things, right? [They’re] not a metal part that I can do whatever I want to, and I can see the desired output at the end of the day.

GM: Tell me more about your smart irrigation project.
DG: Currently in greenhouses, growers check the plants and figure out if they need water or not. [There are] only so many hours a grower can spend in a greenhouse checking all the plants, so it’s based on limited samples that a grower can [use to] determine whether or not they should irrigate. There is some, of course, automation involved that is more like scheduling, so you can water once a day or at a certain time.
What differentiates smart irrigation from the current system is that it tries to irrigate plants when the plants actually need water and for the correct amount they need. For example, if you need to irrigate them for 5 minutes, you irrigate them for 5 minutes. And when they need it. So how do we know when some need it? There are different ways to figure that out.
GM: What are some of the ways you determine this?
DG: There are some legacy sensors that greenhouses use. For example: climate sensors, temperature, humidity, soil moisture sensors, [etc.]. We use them, but also we look at the other technologies that we bring from other industries, like hyper spectral imaging.
The human eye can see wavelengths from 300 to 700-750 maximum. Hyper spectral imaging captures these wavelengths from 750 to 2,500 nanometers. That’s far beyond our capability. And there is important information in those wavelengths through which we can see if the plant is under stress or not. And even better, we can see how much water exists in the plant.
All the legacy sensors do is measure the conditions [around] a plant. What is the surrounding temperature? What is the surrounding humidity? How much water exists in the pot? Based on the ambient conditions, we’re trying to figure out what’s going on inside the plant and hyper spectral imaging allows us to do that. We are looking into the plant with the right device, not trying to estimate how much water is in the plant through other ambient factors. [We’re also using] thermal imaging, which measures the temperature of the plant. All these advances in the system are connected to a very intelligent distribution support system. [This] and the advanced sensory system is what differentiates our system from existing systems.
GM: What do you mean by “intelligent”?
DG: By intelligent, we’re talking about a system that can learn from humans and mimic the decision-making of a human grower. One capability of this system is that when you install it in a greenhouse, it will first just monitor the greenhouse for a certain period of time. It lets the system see what the grower does and tries to learn from the grower and the needs of the plant based on what’s going on through the sensory system.
After some time, if you always trust the [system’s decisions], you can ask the system to take action for you.

GM: Can the system be used with multiple crop types?
DG: It can be fine-tuned to a specific crop. Right now we are working on several crops that have different needs. One of them requires irrigation almost every day. The other one, every three days, [another] every five days. We try to take a range of crops to train our system to learn different irrigation regimes.
GM: When will this smart irrigation system be commercially available?
DG: The first edition, the simpler edition of this system, is planned to be commercialized [in 2017 or 2018]. This system is not going to use the hyper spectral sensors, but the computer is more or less the same.
GM: Have you had the opportunity to test it with different growers at this point?
DG: [At this stage,] we are going to take this to two commercial greenhouses. At this point we are collecting some raw data to fine-tune the decision support system.
GM: What type of greenhouse operation is this geared toward?
DG: At this stage we are just aiming for ornamentals or potted vegetables. Hydroponics is not in our scope because of the obvious reason that it would be two different systems. If weather is going to restrict [water availability], or if you’re going to receive a quota for water, [water] restrictions for floral plants would be applied more seriously than other crops, right? You would cut the water on florals first, then on the vegetables.
GM: Any final thoughts on automation in horticulture?
DG: All I can say is that robotics and automation are [part of] a revolution that is happening right now. So we either keep up the pace and go with it [or], if we resist it, [we’re] going to lag behind. There’s no need to be too resistant to [the] technology. We just need to embrace it and use it to our advantage.
This interview has been edited for length and clarity.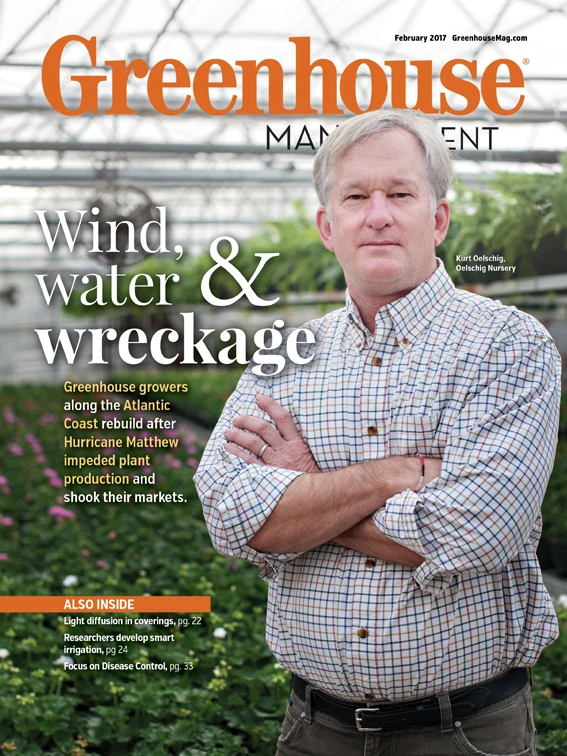
Explore the February 2017 Issue
Check out more from this issue and find your next story to read.
Latest from Greenhouse Management
- Super Charged Moon Juice from Moon Valley Nurseries now available nationally
- 2025 Proven Winners Horticulture Scholarship applications now open
- How to improve inventory and shipping management in the greenhouse
- Leading Women of Horticulture: Anna Ball, Ball Hort, and Terri McEnaney, Bailey Nurseries
- GM CEA HERB Part 2: A guide to increasing the sowing density of culinary herbs
- GM CEA HERB Part 1: Best practices for producing culinary herbs in controlled environments
- USDA fires experts on invasive pests, including Asian citrus psyllid, chilli thrips
- CEA Alliance celebrates bipartisan introduction of Supporting Innovation in Agriculture Act