
Greenhouse Management: To what developments do you attribute the recent increase in interest in automation and moving plants via conveyor systems?
Edwin Dijkshoorn: There is more and more interest in conveyor belt systems because of labor shortages as well as the seasonality of the industry. You’re highly dependent on seasonal labor. They say today in the U.S. there are 9.7 million people unemployed, but nobody seems to be able to find good workers right now. This is not just growers either, it goes across most industries. Wages are also going up, too, and with the cost of some of the equipment going down, there is a much faster return on investment today when it comes to automation technologies.
GM: Why do you think U.S. operations have trended a bit behind their European counterparts when it comes to adopting automation in the greenhouse?
ED: In Europe there is a lot of mono cropping. Many of the largest growers produce only one crop or variety, so the labor cycle is more fixed than over here where a lot of the growers are producing multiple crops in the same greenhouse. The mono-cropping makes automation much easier to adapt to your workflow because your employees are completing the same tasks pretty much every day. And then, again, the seasonality of how we grow here in the U.S., as well as all of the different products that these growers are required to use when they produce a crop for the big-box retailers, it can become quite overwhelming for some of them.
“It is all about eliminating plant touches and people steps where you can, and where it makes sense too.” -Edwin Dijkshoorn
GM: Tell us about your SmartFlo 300 system and how it can enable a grower to be more efficient.
ED: It is all about eliminating plant touches and people steps where you can, and where it makes sense too. Here in the U.S. you have greenhouse operations moving plants and/or products in and out of the greenhouse and into the different production bays at a rapid pace. Normally that requires a train of moveable carts and you have employees picking up the plants two at a time and walking them over to the carts. Once the carts are full, they drive the carts to another bay and they unload and space them back onto the floor. With a conveyor system we can eliminate a lot of those touch points and miles walked. The plants now meet the worker in the workspace. It’s much more efficient and it also provides the grower with peace of mind.
GM: Do you have any parting tips for growers who are thinking about adding conveyors but haven’t done so yet?
ED: Take a 30,000-foot view of your operation and how often you or your workers are touching plants, and how often they are waking to and from plant handlings. Also consider the possibilities. There are a lot of growers expanding right now and building brand new greenhouses, but maybe you are not using the space you already have as efficiently as possible and consolidating crops with conveyors would improve this. Instead of building these big, expensive new greenhouses all the time, you might already have enough space.
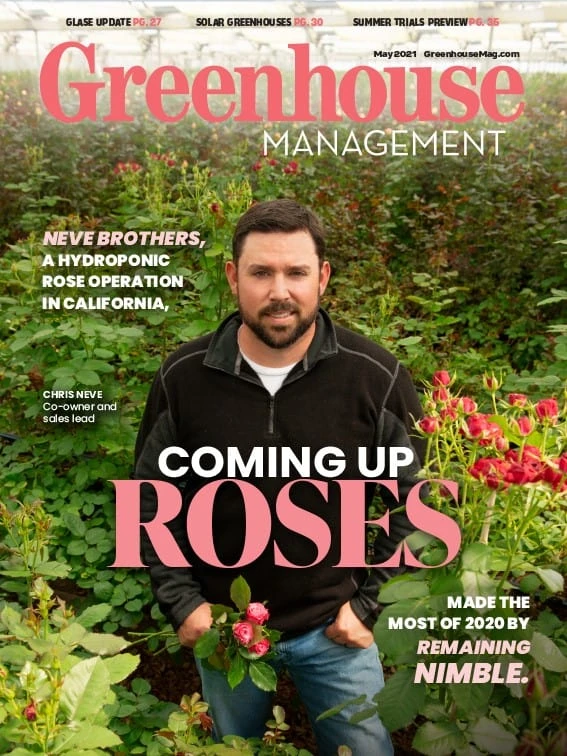
Explore the May 2021 Issue
Check out more from this issue and find your next story to read.
Latest from Greenhouse Management
- CEA Alliance celebrates bipartisan introduction of Supporting Innovation in Agriculture Act
- Dümmen Orange North America celebrating 25th anniversary in 2025
- Illinois Landscape Contractors Association changes name to Landscape Illinois
- 2025 Proven Winners Horticulture Scholarship applications now open
- ICL’s Gemini Granular herbicide now registered for use in California
- Eurazeo Planetary Boundaries Fund acquires Bioline AgroSciences
- Spring Meadow Nursery's Freedom Shelley finds joy in plants
- Leading Women of Horticulture: Dana Massey, Plantworks Nursery