
After World War II, the housing market grew exponentially, and with it, the demand for plants. Growers and nurseries eager to fulfill orders had been limited in their offerings because bare root material covered in a clay-based slurry or plants grown in ceramic pots prone to breakage were not suitable to be transported long distances.
Once plastic plant containers became available, horticulture became one of the fastest-growing industries in modern history. Material could be sent in standard-sized containers and remain intact; their light weight made them easy to transport; they could withstand the elements and were inexpensive to purchase. Today, plastic is the default container used in growing and selling plant material.
In 2019, when I was a member of the Association of Professional Landscape Designers’ (APLD) sustainability committee, I was retained to research and write a paper on the lifecycle of plastic plant containers. In 2020, APLD published “Plastic Pots and the Green Industry: Production, Use, Disposal and Environmental Impacts.”
As designers who are directly involved with purchasing plant material, we were concerned about the negative impact the large quantities of plants (in pots) we order were having on the environment and public health. The issue was approached with vigor and positivity. I couldn’t imagine the unimaginable.

Plastic takes hundreds of years to break down. When it was first produced, this material that was tough, malleable and flexible was all the rage. To a grower, a consistent product with reliable performance is their lifeline. However, the containers (and other products) made with 100% virgin oil take hundreds of years to break down. As they do, chemicals leach into the soil and waterways.
I began visiting growers and asking how they handle their pots once they no longer need them. The default answer was “they get recycled.” Once I began to learn of the challenges to recycling plastic pots, it became clear there was more to this story than I had anticipated. As a matter of fact, others had been trying to make products with them, like Missouri Botanical Gardens with their “Pots to Planks” campaign. Early this century, researchers received grants to study alternative materials, with the hope of discovering reliable “natural” sources.
What I learned was sobering: 95-98% of plastic plant containers are thrown into landfills. Wondering how this could be, I reached out to people in recycling, producers of plastic containers, growers, people that work in our industry, environmental groups and researchers to learn if I somehow was not connecting the dots. Having used thousands of plastic pots over 26 years in business and depositing them in my recycling bin, my heart sank.

Recycling challenges
A number of factors, coupled with changes in China’s laws impacting what we could export, created a perfect storm. The lack of infrastructure to handle the amount of plastic we produce and use brought our country to its knees, with no effective way to respond to ever-growing hills of plastic. Billions of plastic containers are produced every year, and billions are thrown into landfills every year. Back in 2009, 4 billion container/plant units using 1.66 billion pounds of plastic were produced by the container crop industry. The number must be significantly higher today. Presently, we only recycle an average of 5% of the plastics we produce.
Unfortunately, additional obstacles make it even more difficult to recycle plastic pots. In addition to an insufficient number of recycling facilities, issues particular to plastic plant containers add to the challenge. Most pots are made of weak plastics that, at the time I conducted the research, had minimal value as feedstock to produce more products. Our reliance on inexpensive and easy-to-access virgin oil significantly reduced demand for recycled material. Optical readers at recycling facilities cannot detect the color black, often resulting in containers being thrown off the conveyor belt. Soil wreaks havoc with recycling machinery, and to an owner with equipment worth millions of dollars, the risk isn’t worth it. Collecting pots by resin type (the recycling code located on the bottom) and cleaning them is cost-prohibitive to the majority of growers and nurseries. Typical plastic types include HDPE (#2), LDPE (#4), PP (#5) and PS (#6).
Growers are hesitant to use alternative material; what they use works and is reliable. Branding of their products, whether it’s with a different colored container and/or design, is what sets them apart from their competitors. It is easy to understand why a grower would be reluctant to risk the quality of their product. Plus, purchasing new pots every year is less expensive and streamlines production. The thought of changing machinery and investing in other ways to produce their products is understandably taxing.
A study assessing production costs of above-ground nursery systems for various alternative pots (including wood pulp, fabric, keratin and coconut fiber) compared to plastic pots demonstrated the potential to reduce the water, chemical and carbon footprints of greenhouses and nurseries, but the main barrier was cost. The competition and demand for alternative pots did not exist and still doesn’t. (See: Economics of Utilizing Alternative Containers in Ornamental Crop Production Systems. Brumfield, RG., DeVincentis AJ, et al. HortTechnology. February 2015.)



The case for change
A good deal of pressure is coming from consumers. After Sir David Attenborough shared the negative impacts of plastic waste on sea life, a saddened world took a second glance. Bans on the use of plastic bags are becoming increasingly common. Research has shown that consumers are willing to pay a bit more for a product that is healthier for the environment, including plant containers. At this time, those in the industry are hard-pressed to acknowledge how realistic this would be.
Perhaps the most significant impetus for change is legislation that will impact companies’ wallets. Plastics are driving policies. Laws passed in several states require producers of unsustainable and difficult to recycle materials to pay up. Extended producer responsibility for packaging legislation exists in Maine, California, Colorado and Oregon. Producers of products pay into a fund based on the net amount and the recyclability of packaging associated with their products. The fees in turn help fund waste management and infrastructure needs. Mandatory post-consumer recycled content legislation has been enacted in some states, and others are expected to follow suit. A minimum amount of post-consumer recycled content will need to be in each designated product. Some brand owners are taking preemptive steps by increasing PCR content rather than waiting until legislation narrows their marketability. All producers are being forced to rethink the composition of their products. The table has turned. Unlike four years ago when the research was published, the demand for PCR is going through the roof. Now, the concern lies in an insufficient amount of PCR to put into products.
Where does this leave us? The July/August issue of The American Gardener featured an article I was interviewed for that described why we are in this jam and the people I am working with to find answers. They include East Jordan Plastics, HC Companies and Prides Corner Farms in Connecticut, along with many others. Last summer at Cultivate, I presented with HC Companies, Ball Horticultural Company and Monrovia about finding sustainable solutions. The horticulture industry is listening.
More recently, I was pleased to be asked to participate in the Horticultural Research Institute’s new Plastic Task Force. There are other plastics in our industry that will require our attention. For now, decreasing the production of 100% virgin plastic pots is a good start. I have faith that an industry that provides beauty to landscapes can also have a positive impact on the environment. Along those lines, researchers are learning that environmentally conscious gardeners who are incorporating native plants to support wildlife similarly value the importance of recycling their plastic plant containers.
Since the report was published, APLD has created a campaign called Healthy Pots Healthy Planet (healthy potshealthyplanet.org) to educate professionals and consumers about the issue. I have also created a website, sustainableplantpots.org, that educates and provides up-to-date information on ongoing efforts within the industry.
In the next article in this series, I will discuss exciting manufacturer and grower innovations and their impact on the horticultural industry.
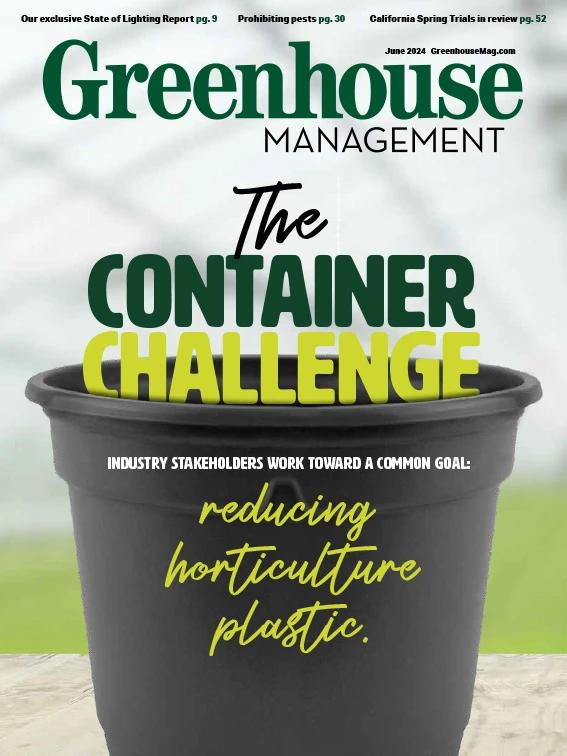
Explore the June 2024 Issue
Check out more from this issue and find your next story to read.
Latest from Greenhouse Management
- Tony Abbas named vice president of sales and business development at Prospiant
- Grant awarded to test western U.S. wood species for use as wood fiber potting substrate
- Pennsylvania Horticultural Society announces 2025 Gold Medal Plant winners
- GIE Media Horticulture Group wins five regional 2025 Azbee Awards of Excellence
- Terra Nova Nurseries introduces rust-free and disease-resistant heucherella
- John T. Nickel, founder of Greenleaf Nursery Co., passes away at 89
- Three tours offered at 2025 Farwest Show
- Garden Media Group announces sixth annual Women in Horticulture Week