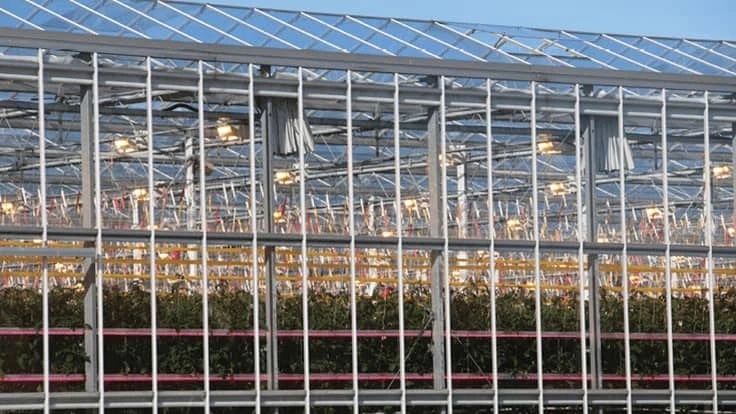
_fmt.png)
Commercial greenhouse growers have new lighting technologies top of mind.
This year’s State of Lighting Report shows more than two-thirds of growers surveyed plan to upgrade or invest in new lighting systems over the next three years.
Growers rely on supplemental lighting for a multitude of reasons, chief among them being additional lighting during periods of low light (33%) and day length extension (30%). Currently, light-emitting diodes (LEDs) are the top choice among this group with 79% reporting usage, while high-pressure sodium (HPS) (50%) and fluorescent (29%) fixtures round out the top three.
We reached out to three growers planning to make a significant investment in either upgrading or installing new supplemental lighting in the greenhouse to see what’s driving their decisions.
Training tomorrow’s grower
The Abilities Connection (TAC) operates a 3,000-square-foot greenhouse an hour southeast of Columbus, Ohio. TAC Farms is a member of the Growing Opportunities Partnership, a coalition of 10 hydroponic greenhouses nationwide whose primary focus is vocational rehabilitation for adults with developmental disabilities.
Their goal is to teach a well-rounded horticultural skillset that positions graduates for job placement in greenhouses throughout Central Ohio.
Currently, the operation plants and harvests lettuce crops on a six-week production cycle. TAC uses three forms of supplemental lighting in the greenhouse — LEDs, HPS and fluorescent — to provide the trainees with as well-rounded a growing experience as possible.
The group applied for 14 different grants over the past year, hoping to secure funds to expand the growing operation to “either double the size of the existing hydroponic arrangement, expand indoors in about the same footprint using a dry fog system or add two 40-foot containerized hydroponic units,” says Lou Driever, who coordinates hydroponic operations.
“The simplest way to expand production is increasing the number of grow sites,” Driever says. “We can alternatively increase production by increasing the growth rate or harvestable mass of the produce. With the future expansion, I believe we will go all red/blue LED. As part of the learning curve, we will be specifying the frequencies to ensure those are optimal for leafy greens.”
Driever says he’s intrigued by recent developments in pulsating light arrays designed to maximize photosynthesis in the farm’s indoor lettuce crops, although the operation’s size means that not all technologies will “pencil out” in terms of ROI.
Still, a recent grant-funded investment in new red/blue spectrum LEDs in one of TAC Farm’s indoor grow rooms left a good impression on Driever. The addition quickly boosted yields by 50% in a space that had been plagued by shadows and uneven coverage. That one did end up penciling out, after all.
“We are eager to act as a testbed for lighting applications,” he says. “To that end, we can work with vendors on their beta testing, identifying any potential glitches that may arise before they spool up to field them en masse.”
All signs point to staying put
Dave Demarey grows off-season, flavor-bursting indeterminate tomatoes in a 5,000 square foot greenhouse on the outskirts of Westhampton, Massachusetts.
In New England greenhouse production, supplemental lighting is “the name of the game,” he says, noting that his current setup deploys double-ended High-Pressure Sodium (HPS) fixtures.
“I just finished an expansion [with HPS] and now we’re looking at extending it into another building, where we’ll probably have to lower the ceilings a little bit first,” Demarey says. “I’m really struggling right now on whether to go to LEDs or stay with the HPS.”
The issue, the grower says, is a bit of a conundrum. In the area he wants to expand lighting into, the fixture mounting height is a bit higher than recommended. He could drop the ceiling height, or he could select a light powerful enough to penetrate down into the canopy and somewhat limit extensive vertical stretch. After all, in greenhouse tomatoes you do want some stretch.
“My process is actually quite a bit more research-based than that,” Demarey says when asked if he will rely on word-of-mouth when making his lighting buy. “I’ll go through as much of the research that’s out there that I can get my hands on, and then I’ll add in some of my own direct experience.”
When it comes to his own variety of indeterminate tomatoes specifically, he has learned that the end of season differences when comparing the two types of lighting are minimal.
“The grams [of yield] per watt are almost identical, and to be honest right now the cost factor remains in favor of the HPS fixtures,” Demarey says. “If you base it solely on the spectra quality and actual production between the two, there is no observable difference between LED and double-ended HPS, they’re right there alongside each other.”He does say that LEDs in fact have a slight (10% or less) yield advantage over the HPS he is using currently, but “the newer HPS are very broad spectrum, so their relative efficiency is really high.” Demarey’s HPS fixtures also put off a slightly greater measure of heat, a crucial ancillary benefit in the brutal New England winters, when those extra three degrees of heat — which Demarey measures and tracks — on average make a major difference on his heating bill.
“Look, I think a lot of these new LEDs are really great, but I think the big thing that stops everyone going whole hog into the LED market is the up-front investment cost,” Demarey says. “I can put together a nice HPS setup for my greenhouse for about 22 cents a watt. Something similar but with LEDs would be $1 per watt, minimum.
Doing due diligence
Snethen Farms in Montrose, Missouri, plans to expand beyond its current high tunnel and fluorescent tube lighting setup in the next 12-18 months with a high tech, climate-controlled greenhouse, as well as some hydroponic growing systems and more high tunnels.
For his part, owner-operator Michael Snethen is tiring of the constant adjustments needed to make sure his fluorescent tube fixtures remain directly above the canopy of his vegetable transplants.
Any slip-up and young seedlings emerge from spring propagation too leggy and not as attractive to the scrutinizing buyers of commercial starter stock.
“My main agenda is to come up with better grow lights to propagate my vegetable transplants,” the grower says. “I also want to supplement a few early tomatoes and peppers with a few hours of lighting until the day length is sufficient.”
Up to the present, the initial cost of investment has discouraged Snethen — a newer indoor produce grower — from pulling the trigger on some new LED or HPS fixtures.
“I don’t really know where to start (with supplemental lighting),” Snethen says. “I’ll be doing a considerable amount of research this fall and into the winter.”
That process will entail Snethen leaning heavily on word-of-mouth referrals from other growers, as well as a bit of social media and online product review sleuthing.
“The advice of fellow growers is almost exclusively the best,” he says, adding that he believes a grower subsidy program for supplemental lighting would “really give it a boost.”
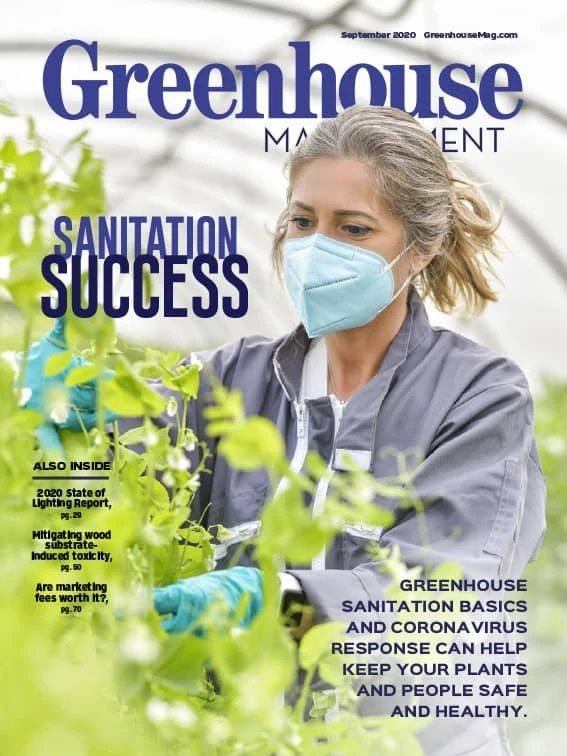
Explore the September 2020 Issue
Check out more from this issue and find your next story to read.
Latest from Greenhouse Management
- North Carolina Nursery & Landscape Association announces new executive vice president
- Plant Development Services, Inc. unveils plant varieties debuting in 2025
- Promo kit available to celebrate first National Wave Day on May 3
- Applications now open for American Floral Endowment graduate scholarships
- Endless Summer Hydrangeas celebrates 20 years with community plantings
- Invest in silver
- Garden Center magazine announces dates for 2025 Garden Center Conference & Expo
- USDA launches $2 billion in aid for floriculture growers