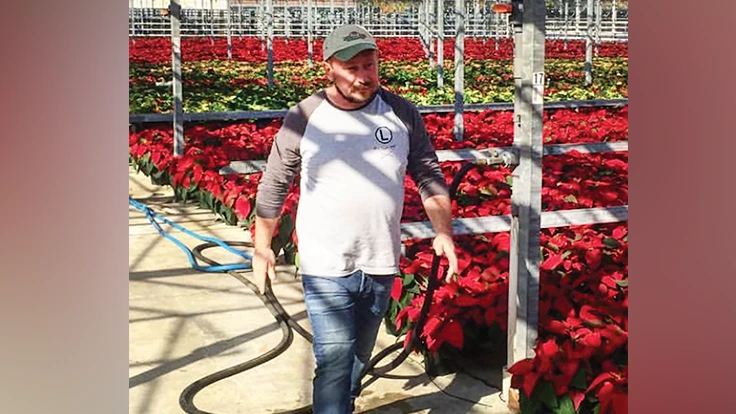
Photo courtesy of Artur Zych

The one constant Artur Zych expects to see in the greenhouse industry is change. From shifting seasons to advancing technologies to new plant and product introductions, every day is a new challenge for growers — and that’s what Zych loves about it.
“Growers can’t be afraid to change because change is always happening,” he says. “That’s one thing that’s certain.”
As head grower at Lennon Farm Greenhouses in Tabernacle, New Jersey, Zych works to stay current with shifting industry trends in order to produce the highest quality plugs and finished plants for wholesale customers. By following his curiosity to explore improved plants and processes, Zych helps Lennon Farm move ahead.
“That’s what keeps me motivated — knowing we bring joy to people,” he says. “When you see a beautiful plant, whether it’s a finished product or perfectly uniform plugs being shipped to the customer, that’s the most enjoyable moment of a grower’s life, knowing these crops will make somebody happy.”
Learning to grow
Zych grew up surrounded by plants in Poland, so pursuing a career in the green industry was a natural choice. After studying agronomy at an agribusiness university in his home country, he wanted to keep learning more. So he applied for The Ohio State University International Exchange Program, and arrived in Columbus 20 years ago. He quickly “fell in love with greenhouse growing,” and built his career around it.
He started out at Metrolina Greenhouses, where he learned the ins and outs of plug production. After a couple of years there, he moved to Plainview Growers in New Jersey to get a feel for finished plant production. About a decade later, in March of 2013, Zych joined Lennon Farm, where he combined both these experiences to oversee the production of plugs and finished plant material.
"When you see a beautiful plant ... being shipped to the customer, that's the most enjoyable moment of a grower's life, knowing these crops will make somebody happy.”
Zych feels lucky to have worked at companies where the owners have taken him under their wing to teach him more about the industry.
“They have been like family because they treat their employees like family,” he says. “Since I was far away from home, it was a great experience to find mentors like that.”

Evolving tools
Driven by a passion to keep improving, Zych continues to explore new tools and technologies to enhance Lennon Farm’s operation.
“My job has evolved from just following the growing protocols they had to improving with new protocols and new techniques to ensure that our quality specs are met,” he says.
For example, Lennon Farm had just built a brand-new 60,000-square-foot greenhouse before Zych joined the company, and they implemented boom irrigation soon after. Zych immediately set out to make the most of the new equipment.
“Working with our boom supplier, I designed a special bar that I connect to my injector, and then I use that to apply PGRs,” he says. “Believe it or not, we humans make errors. When you spray manually, especially PGRs, you can miss spots — so spraying with a boom improves the crops.”
Adjusting applications
Zych constantly adjusts Lennon Farm’s application programs as he explores new chemistries to improve plant health and address customer concerns.
“Even though we are not OMRI certified, I do like to be conscious of what I’m applying. I don’t use hard chemistry on our vegetables, so our customers can be reassured that it’s safe to consume these crops,” Zych says. “Biological control agents are getting more popular because the general public is getting more educated about neonicotinoids, so we’re trying to be more cautious and use more BCAs.”
Recently, Zych started dipping plugs before they get transplanted. He customizes special blends of insecticide, fungicide and PGRs to dip plugs into — giving plant material better coverage at a lower cost than drenching.
“So far this year, I’m very happy with the outcome,” he says. “It saves us money (compared to) the dollar value of the chemicals we would use if we had to do these same applications as drenches. I know chemical companies won’t like me saying this, but every penny counts. We’re trying to be mindful of cost because the competition is tough.”
Running a tight ship
Like most growers today, Zych’s biggest challenge is finding enough talent to meet demand, especially as the economy improves.
Lennon Farm’s production space spans 160,000 square feet under glass, 80,000 square feet of rollouts to expand the production area in the spring and 25 acres of outdoor production space for fall crops and grasses.
“For as big as we are, we only have 16 people working. There are only two growers right now,” says Zych, who’s currently down one grower and searching to fill the opening.
The small team size allows him to be more hands-on as head grower, and it forces him to be innovative to maximize limited resources.
“We’re running a rather tight ship,” Zych says, “so we need to use the technology there is to work smarter, not harder.”
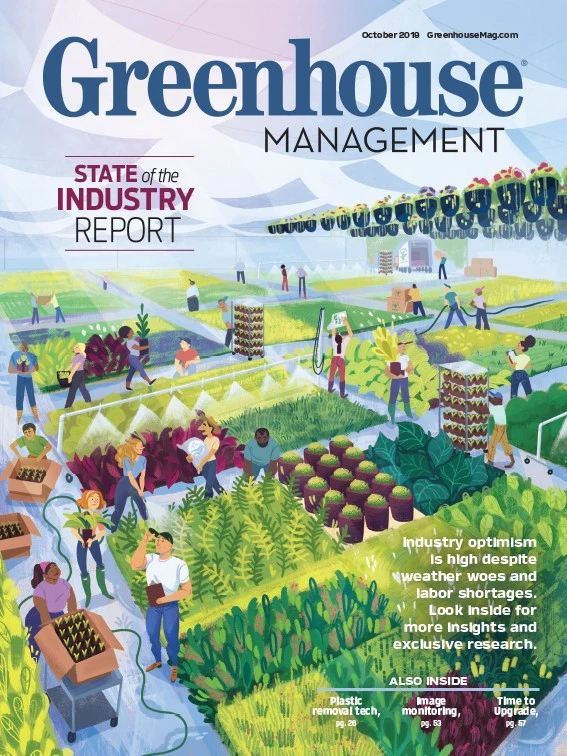
Explore the October 2019 Issue
Check out more from this issue and find your next story to read.
Latest from Greenhouse Management
- CEA Alliance celebrates bipartisan introduction of Supporting Innovation in Agriculture Act
- Dümmen Orange North America celebrating 25th anniversary in 2025
- Illinois Landscape Contractors Association changes name to Landscape Illinois
- 2025 Proven Winners Horticulture Scholarship applications now open
- ICL’s Gemini Granular herbicide now registered for use in California
- Eurazeo Planetary Boundaries Fund acquires Bioline AgroSciences
- Spring Meadow Nursery's Freedom Shelley finds joy in plants
- Leading Women of Horticulture: Dana Massey, Plantworks Nursery