
Like crocuses bursting from the ground, the spring rush is coming and unstoppable. But instead of wringing your hands and worrying you might not be able to fill all the orders piling up on your desk, take a few tips from growers on how to slide through the season with less hassle.
1. Start preparing in the off-season.
“Being prepared is key,” says Kathy Donahue Nass, CFO and manager at Donahue’s Greenhouses in Faribault, Minnesota. “Think of any small or large thing you can get done in the off-season that will help you. One thing we do is go through all of our signs and get them updated. We sort them alphabetically so they are easy to find when we need them. This also requires us to update our price list for our plants ahead of time, a good thing to do.”
Bill Swanekamp, president of Kube-Pak in Allentown, N.J., believes proper time management in the spring is always “essential,” but not all growers are good time managers. “It is up to the executive management of the company to identify what tasks are not being managed efficiently by the growers and provide direction or more software tools to get things done in a timely fashion,” Swanekamp says.
He says there are software improvements available that can make the entire shipping process easier and more efficient. “Also, make sure you have enough carts and trucks to handle the busiest days,” he says.
Time management is also crucial for Donahue Nass’ business. “Setting goals for accomplishing tasks in the off-season is important,” she says. “It’s easy to put things off when it’s not crunch time. But by setting goals and completing them it really sets you up to be better prepared for the busy season.”

2. Use your staff wisely.
Wise use of your staff can also pay big dividends when things get hectic. Donahue Nass has found that when there are big projects that need to be completed, it’s helpful to get a big crew on the task rather than having just a few employees “struggle” to get it done.
“We also find that if we’re resetting some displays [in our retail department], it’s best to start and get these done before we open,” she says. “If you try to do this when the store is open, the many interruptions just stretch the process by hours.”
3. Automate as able.
Nola Wagner, president of Wagner Greenhouses and Garden Center in Minneapolis, believes automating some processes can certainly save time. “Automating is wise if there are funds to purchase equipment to manage tasks, such as seeding machines, a replug automatic conveyer, a moisture control unit with booms, a cutting belt conveyer, automatic computer systems for picking and shipping documents, and many more,” Wagner says.
Donahue Nass’ business has “automated” one process that was an “unbelievable time consumer”: putting boxes together. “We used to have to fold and staple the boxes. This required a person to work almost full time just making boxes for the month of May. We redesigned our boxes so they just fold and a tab holds it together. We now do not need one person dedicated to making boxes. Our clerks are able to make them when they are not busy. They like having something to do, and it frees up the box maker to work in the greenhouse.”

4. Value your workers.
Keeping employees happy during a stressful time is also paramount to a smooth operation. “Employees are generally happy when they are making good money,” Swanekamp says. “Even though it is not required, we pay time-and-a-half for all work done on the weekends throughout the year. This is especially valuable during the spring season, because the workers see the fruits of their hard work.”
Donahue Nass likes to create a “team atmosphere” on the weekends by serving lunch to all of the company’s employees. “As a family business, we feel this is great for our employees,” she says. At Donahue’s, staff unites for a simple 30-minute lunch that usually consists of sandwiches, chips, salad, cookies and the like. “They go back from that break refreshed and ready to work for another four to five hours,” Donahue Nass says.
Swanekamp says it is smart to have a list of former part-time workers that can be called in as backup when needed (perhaps when one or more employees call out sick during crunch time). “We have a large group of part-time former employees that work only in the spring and are a tremendous asset to a successful spring season,” he says.
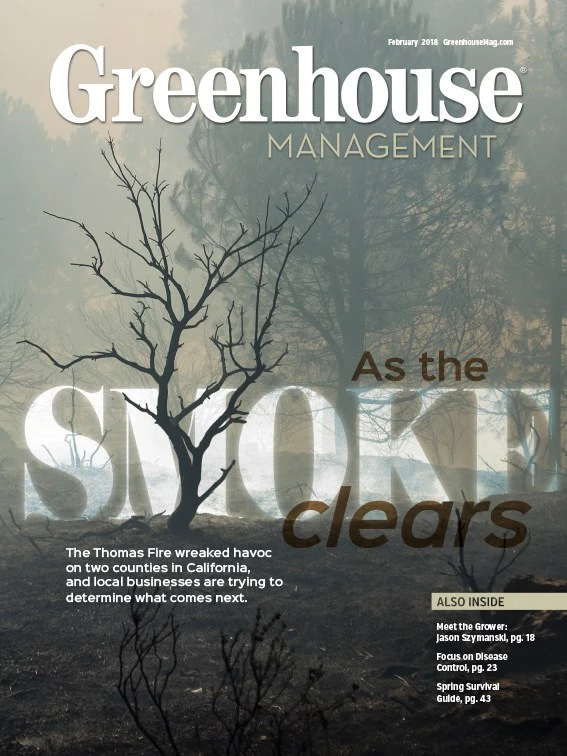
Explore the February 2018 Issue
Check out more from this issue and find your next story to read.
Latest from Greenhouse Management
- 2025 Proven Winners Horticulture Scholarship applications now open
- How to improve inventory and shipping management in the greenhouse
- Leading Women of Horticulture: Anna Ball, Ball Hort, and Terri McEnaney, Bailey Nurseries
- GM CEA HERB Part 2: A guide to increasing the sowing density of culinary herbs
- GM CEA HERB Part 1: Best practices for producing culinary herbs in controlled environments
- USDA fires experts on invasive pests, including Asian citrus psyllid, chilli thrips
- CEA Alliance celebrates bipartisan introduction of Supporting Innovation in Agriculture Act
- Dümmen Orange North America celebrating 25th anniversary in 2025