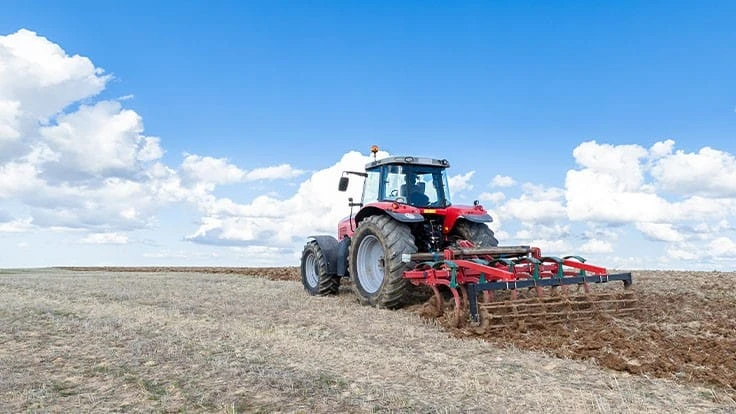
Photo courtesy of Abobe Stock
With nine locations across Northeast Ohio and more than 7,000 varieties of plants and flowers, Petitti Garden Centers must do all it can to maintain an efficient production flow. They do so with the help of equipment and methodological approaches to labor.
Hernie Rosado, production manager at Ridge Manor Nursery, one of several Petitti growing operations, says a lot has change in his 12 years of employment. At first, the nursery had 40 employees at peak season and only sold 40% of what they’re selling today. Now, they have a total of 100 employees — office workers, drivers and field personnel — and according to him, sales have increased about 60 to 70%. He credits that to their labor tactics.
“It’s not because of the number of employees, it’s because we’ve put certain systems in place,” he says. “Timing is everything. We track how long it takes to pull orders, how long it takes to process and ship out, how long it takes to get to the furthest part of the nursery to another section, or from this section to that section. We’re able to save time and move right along to get the jobs done.”
With the lean flow system — a hodgepodge of approaches used to maximize productivity — team members are able to reduce extra travel, manual labor and wasted time that may have occurred otherwise.
Since the farm is divided into seven sections, Rosado says they’ve organized crops based off their bloom time to minimize unnecessary walking. For example, since forsythia blooms in early spring, he says 95% of that crop is sold early. Because of that, Ridge Manor has that crop at the furthest point of the nursery. Crops that are sold each week, like boxwood, spirea or roses, he says, are positioned closer to one another.
“We don’t have the down time to go back and forth, back and forth,” Rosado says. “If I had the popular plants at the furthest part of the nursery, we’re going to waste twice as much time just walking.”
Equipment-wise, their use of machines has cut down on unnecessary work as well, but most importantly, on labor costs.
“We bought two rice hull machines once that were $16,000 a piece, but it freed up four guys to do other things,” he says. “The machines basically paid for themselves before the end of the season.”
Although machinery is very helpful, Rosado notes some cons. According to him, horticulture equipment falls into 1 or 2% of the available machinery, and since companies aren’t making a lot of equipment for the industry, he says the biggest problem is being the “guinea pig,” and lacking a user’s manual when issues arise.
Even so, Rosado recommends equipment to every large grower.
“They’ll still need a personal touch but since labor costs go up every year and it’s hard to find help in this industry, we’re constantly looking at ways to make things easier — easier on ourselves and easier on the guys too. We don’t want anyone hurting themselves or breaking their backs. In the same sense, if this machine can do this, where else can I put this guy? And, machines are exactly that — machines. They can turn all day, they don’t each lunch, they aren’t slow at the end of the day and there’s no worker’s comp,” he jokes. “It’s definitely worth it.”
Latest from Greenhouse Management
- CEA Alliance celebrates bipartisan introduction of Supporting Innovation in Agriculture Act
- Dümmen Orange North America celebrating 25th anniversary in 2025
- Illinois Landscape Contractors Association changes name to Landscape Illinois
- 2025 Proven Winners Horticulture Scholarship applications now open
- ICL’s Gemini Granular herbicide now registered for use in California
- Eurazeo Planetary Boundaries Fund acquires Bioline AgroSciences
- Spring Meadow Nursery's Freedom Shelley finds joy in plants
- Leading Women of Horticulture: Dana Massey, Plantworks Nursery