
The best fertilizer and pesticide is the gardener’s shadow, and that is especially true where pesticide use on cannabis is tightly restricted or prohibited. Good cultivation directors develop pest management programs that allocate a significant amount of time into staff scouting in order to catch outbreaks before they become disasters. The key to effective scouting, it turns out, is just a little SOAP.
A core structure
Whether performed by a lone grower or many hands in a commercial facility, pest management boils down to obtaining information, followed by understanding and acting on that information. This is how most process-management systems are structured. The acronym “SOAP” is a simple way to remember what a pest scouting program should look like.
Before Kerrie was a horticulturist and Greenhouse Management sister publication Cannabis Business Times columnist, she was a nurse. It was as a nurse that she was introduced to a human diagnostic protocol called SOAP, which stands for: Subjective, Objective, Assessment and Planning.
In nursing, SOAP is aimed at helping students diagnose and react to human maladies. Kerrie recognized the principle could be applied to cultivation to not only teach new hires to become effective scouts, but also to form the core of the pest management programs we designed for our clients when regulated cannabis came around.
Here’s how SOAP breaks down:
S – Subjective symptoms provide clues to what problem is being observed. The clues may be weak (“There’s a discoloration”) or strong (“This frass proves pests are present”), but they do not allow for definitive pest identification. Plant growth issues can be difficult to diagnose, given that numerous problems produce similar symptoms, and an under-fed plant can be symptom-free, yet still not produce the desired yield. Pictures are the best way to capture visually noticeable subjective symptoms. They can be shared so that multiple people can help with identification, if necessary.
O – Objective symptoms are definite. When a pest is seen that matches the description for twospotted spider mites, for example, that is an objective observation. Measurements and locations are also objective. The infected area where pests were found can be indicated on a scouting map. Subjective and objective symptoms together provide a pest-pressure snapshot, and that picture is what is used to determine if action is required to keep pests and diseases within operational limits.
Scouts need pest identification training, but they don’t need to be entomologists to be good at spotting and identifying pests and diseases. However, an operation does need to provide staff with reference material so that everyone consistently receives the same training. After identification, the pests’ location and infestation’s extent should be documented to make a pest-pressure assessment.

When this data is gathered over time, it paints a dynamic picture. By capturing data daily, the speed at which pests go from unseen to uncontrollable becomes breathtakingly clear and will prove how important intensive daily scouting is to keep pests at bay.
Operation managers ask daily questions about pest pressures such as, “How much of it is there? Is it spreading? Where did it come from?” Subjective and objective symptoms serve as the primary answers to these questions. To acquire that data, someone must spend time with the plants and document what he or she finds.
A – Assessment of symptoms can be performed by scouts or by the head grower, as long as the assessment outcome is communicated appropriately throughout the organization. Smaller producers don’t have four levels of management and a staff of 50, so one person is responsible for pest management and he or she must conduct the assessment. Large-scale producers have multiple scouts feeding them information, so the assessment process needs more structure to aggregate the inputs for inspection and analysis.
A post-scouting team meeting where all scouts share what they have encountered is the easiest form of assessment. The assessment is made there and then by whomever or whatever group has responsibility. More detailed assessment processes can be implemented when required, but assessment slows response time, so keep the process dynamic.
Assessment is where scouting data is weighed to determine the level of exposure to the company and what, if anything, needs to be done to reduce that exposure. This is where having experience with different problems helps growers anticipate whether a problem is getting worse or better.
Data means nothing without a reference, whether that reference is research-driven or anecdotal. An outbreak that covers 5 percent of the canopy may be a manageable incident if experience has shown that treatments at this infestation level have been proven generally effective. On the other hand, if five-percent infestations have been seen before and the results were negative, then the team is looking at a time-sensitive (and potentially huge) problem. Assessment is where the grower’s experience pays dividends.
The best example of that payoff is when botrytis is found. Botrytis spreads so fast that the response to it must be automatic. Botrytis demands careful and immediate removal of obvious infected plants, and the remaining crop must be harvested quickly and brought under quarantine into a dry environment until it is cleared of any further infection. Botrytis doesn’t respect growing schedules. Expect to lose yield because to cut losses, the crop is coming down before it can finish.
Experience informs growers on what pest population levels can be present without posing a threat to supply or quality. That level may be different from operation to operation. Flower production demands the lowest pest levels, as appearance is a key quality metric in that market segment. Plants headed to extraction can tolerate higher infestation levels, as appearance is less important. In extraction, the limiting factor may be more of question of: At what infestation level does a powdery mildew outbreak create contamination issues in extracted product?
P – Planning is the final step in the protocol. At this stage, managers ensure that any deviation from normal control practice is properly planned and communicated before it is executed. If a new knockdown pesticide is to be tried on an outbreak, all responsible parties — from operations, cultivation, safety and compliance — must have a say. The idea behind including so many people is to leverage everyone’s experience and to instill a feeling of part ownership of managing the operation. The planning process itself can be evaluated by keeping track of mistakes made during planned production changes and emergency actions.
Implementing SOAP
Whether it be a piece of paper, white board or software application, the SOAP protocol captures data about what is seen on the production floor. Scouts need to be educated in what they are looking for before they can begin scouting. That education should be part of the operation’s new staff onboarding program. Intensive scouting requires scouts to be able to quickly and easily document what they see and where. The basic documentation consists of a map on which the scout indicates the area of infestation found and the pests or symptoms observed. Supporting that mapping is a cheat-sheet with pests, diseases and symptoms.
Scouting a cannabis room is a lot like searching for a needle in a haystack; finding pests before they can damage the crop requires laser focus. If a scout always walks through a room in one direction, he or she sees only one angle of the crop and can miss symptoms that might be seen if walking the other way.
Scouts need to be educated in what they are looking for before they can begin scouting.
Time also influences a scout’s effectiveness. If a scout is pressed for time, there is a good chance he or she might rush the scouting process in order to complete other tasks by day’s end. Symptoms cannot be seen if the scout doesn’t look, so time is gold in scouting. Pest management education is the best way to equip staff with the background needed to perform stellar scouting before turning them loose.
Get clean, stay clean
Getting pests and diseases under control is hard work. When clients have shown us bad outbreaks, our first question is always, “How did they let that get out of control?” The answer almost always has been, “We didn’t see them,” or, “We didn’t realize how bad it was.” In cultivation, those are unacceptable answers — especially when all it might take to clean up pest problems is a little SOAP.
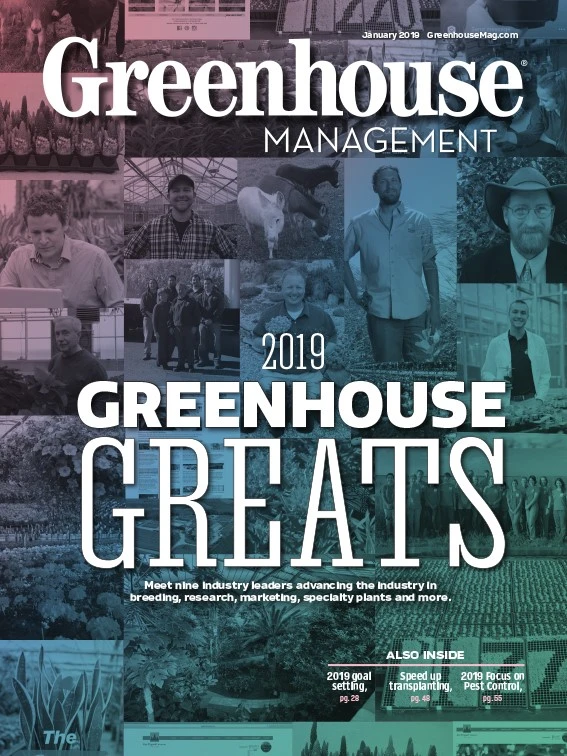
Explore the January 2019 Issue
Check out more from this issue and find your next story to read.
Latest from Greenhouse Management
- 2025 Proven Winners Horticulture Scholarship applications now open
- How to improve inventory and shipping management in the greenhouse
- Leading Women of Horticulture: Anna Ball, Ball Hort, and Terri McEnaney, Bailey Nurseries
- GM CEA HERB Part 2: A guide to increasing the sowing density of culinary herbs
- GM CEA HERB Part 1: Best practices for producing culinary herbs in controlled environments
- USDA fires experts on invasive pests, including Asian citrus psyllid, chilli thrips
- CEA Alliance celebrates bipartisan introduction of Supporting Innovation in Agriculture Act
- Dümmen Orange North America celebrating 25th anniversary in 2025