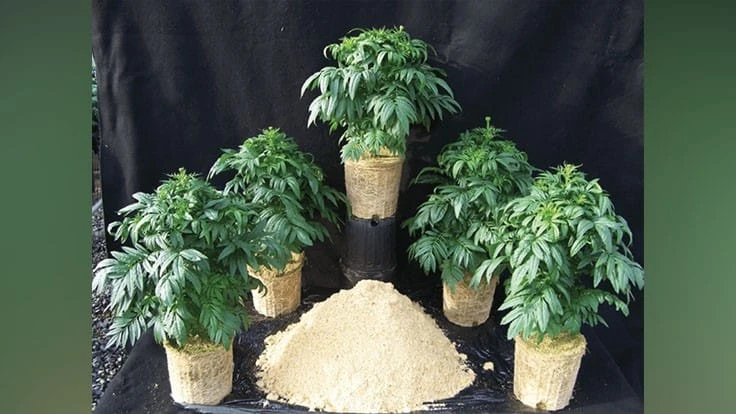

Reduced plant growth in fresh wood-based substrates has been attributed to several factors including fertility, irrigation, and most commonly toxins (phytotoxicity).
Evidence of this condition has been published and observed for decades when growing in substrates that contain certain types and percentage of fresh (non-composted) and untreated wood materials.
The wood chemicals (secondary metabolites) responsible for inhibiting seed germination and stunting herbaceous plant root and shoot growth, are vital to the health and defense of trees while standing, but they need to be removed or rendered harmless before being used as a substrate to grow plants. These wood chemicals, known as extractives, are a group of compounds (either volatile or soluble) that vary in type and concentration depending on tree species and origin (region of growth).
Extractives are found in higher concentrations in older trees (thicker bark and more heartwood) than in younger trees (thinner bark) and the amounts in any given tree can fluctuate with different seasons of the year. Additionally, the amount of potentially harmful extractives is higher in tree bark and heartwood compared to softwood.
With these as well as other factors being known, tree species, tree age, harvest season, and the presence of bark should be considered when selecting or acquiring wood feedstocks to produce substrate materials.

Strategies for removal
Wood extractives, which research has shown to be less harmful to woody plants (rooted nursery liners for example) compared to herbaceous plants (seeds, plugs, transplants), can be successfully removed or mitigated by one of several strategies.
Better yet, once toxins are removed, growing quality plants in 100% wood substrates is possible as seen in Fig. 1.
Note that there are many variables to each of the following procedures that cannot be fully addressed in this article, but more information will be released in the future as research continues.

Wood processing method
After feedstock selection, the type and method of processing that wood chips undergo is a critical step in removing harmful extractives.
There is roughly a half dozen commercial machine types used (globally) to produce wood substrate products but three are most common: hammer mills, single or twin-screw extruders, and twin disc refiners. Each of these technologies function differently to reduce/separate wood chips into fibers or smaller wood chip particles.
Each of the methods also differ in their initial set-up cost, operating costs, annual maintenance costs, the range of size and moisture content of wood chips they are able to process, and ability to produce different particle sizes and shapes.
The primary features of the different machines that are responsible for the reduction or elimination of harmful wood extractives are heat generation, pressure, friction, and/or dry or wet processing. Heat and pressure (together or separate) are known to drive off (volatilize) wood extractives into the air. Exposure to a water or chemical solution bath for some period of residency time has also been shown to effectively solubilize certain extractives from wood chips.
Either by one, or both of these factors, wood chips can be refined to smaller particle sizes suitable for substrates and at the same time have their inherent chemicals removed in the process. Let’s take a look how the three machine types differ.
Hammer mills, the cheapest and most common of the methods, are used universally for processing many types of organic materials. Hammer mills operate by pulverizing particles with swinging hammers (or knives) until the material is reduced in size enough to pass through a perforated screen (Fig. 2A).
Wood chips typically need to be dry (under 40% moisture content) when processed in a hammer mill to prevent clogging. During the operation of the mill there is some heat generated, but the amount and extent is mostly proven negligible in significantly volatilizing wood chemicals. There is, however, some minimal chemical volatilization occurring as a direct result of the reduced (smaller) particle sizes being exposed to the air and dried during processing.
The heat that is generated in a mill depends on the moisture of the wood chips being processed, rpms and operational speed of the machine, and time of year of processing. Twin-screw extruders (Fig. 2B) have opposing screws that apply mechanical energy to wood chips which crushes, shears, and squeezes them to separate the wood fibers. During the process the pressure can rise to 500 kilopascals (~75 pounds per square inch – PSI) and the temperature can reach 210 – 230 °F (100 – 110 °C). After passing through the screws, a sudden “relaxation” of friction and pressure creates a steam explosion which results in further tearing of the wood fibers.
The friction heat and pressure effectively volatilize many wood extractives, thus mitigating the phytotoxicity of the end product (substrate) even when used immediately (Fig. 2C-D).
The twin-disc refiner is a large disc mill operating at high speed and pressure (+/- 4000 kilopascals = ~580 PSI) with internal temperatures reaching 220 – 400 °F (110 – 200 °C). This technique often has a water bath phase where wood chips are pre-soaked in a pressurized heated vessel for several minutes before being forced through the rotating discs. In this scenario, there is a solubilization and volatilization phase of the process which are effective at removing harmful wood extractives.
Lastly, the practice of co-refining wood chips with some percentage or peat, bark, or other material has been shown to be effective in further reducing (by dilution) wood phytotoxicity in the substrate material produced. Co-refining wood with other materials can be done with any of the three machine types mentioned above.

Substrate preconditioning
These methods are aimed at hammer-mill processed wood products as a result of the lack of sufficient heat/pressure generated in the mill.
Extruded or disc-refined commercial wood substrates have not been shown to need additional corrective measures to reduce toxins.
For hammer-milled wood substrates, aging has been shown to be the best and most effective method of reducing green wood toxins. Aging of wood can occur at different stages including the storage of harvested trees for a period of months prior to processing (Fig. 3A), aging of wood chips (under shelter preferred; Fig. 3B), aging of processed wood substrate outdoors or under shelter (Fig. 3C), or processed substrate aged in totes (Fig. 3D).
Aging, often called “seasoning”, of wood chips in piles for two weeks has been shown to be as effective in reducing toxins as aging whole logs for six months. The season of the year that aging occurs also will affect the duration needed to effectively mitigate the wood toxins due to temperature and rainfall fluctuations.
Aging of processed substrate in totes has received the most research over the past decade with the general recommendation that 4-6 weeks be allowed for the process. Longer periods of time do not negatively affect the quality of the end product.
However, aging large piles of fresh pine wood (sawdust or processed fiber) similar to pine bark substrates has not been perfected at this time and seems to be less consistent, more time consuming, and more variable than other forms of aging.
Preliminary research suggests that processed fresh pine wood substrates can also be dried at high temperatures very quickly to reduce (volatilize) harmful chemicals (Fig. 4A), although the exact temperature and duration needed are not yet fully understood.
Industrial dryers/drying can add an additional cost to the substrates, but based on how cheap hammer milled substrates can be produced, this added expense still makes this a viable economic option.
Other practices that have been explored with varying levels of effectiveness include the addition of charcoal, brown coal/lignite, or pulverized biochar products to wood substrates to bind the toxins, preventing them from affecting plant growth (Fig. 4B). Substrate steaming (pasteurization) in soil carts (Fig. 4C) and substrate washing or soaking in cold and hot water have also been investigated but the results are varied and inconsistent.
Additional strategies explored in reducing wood toxicity include the inclusion of peat, bark, or coconut coir (non-toxic substrate materials) to wood, thus reducing the wood percentage in the final substrate (Fig. 5A). This has been the most practiced strategy over the past decade since hammer milled pine substrates were first investigated (2004 – 2008) to be used at 100%. Since then, the most common wood product inclusion rate has been 20–40%, thus reducing the threat of green wood toxins. Research continues on this topic and is needed before more hammer milled wood products are used reliably and consistently.

Production practices
If fresh hammer milled wood materials (or pine sawdust, though not recommended at this time) are used in substrates without any preconditioning, there are practices that could help reduce plant stunting and other growth defects.
The most proven effective way to reduce wood toxins in containers is to leach them with water. Leaching containers with clear water frequently for a week (or as often as possible without imposing more detriment to the plants) has been shown to be effective in removing the toxins from the container (Fig. 4D).
Leaching of substrate-filled containers with over-head irrigation prior to planting has also been successful for some growers. Experiments have been conducted on various container sizes, leaching frequencies, drainage rates, and limited or stratified wood layers and volumes (Fig. 5C) to better understand how to solve production problems with wood substrates if they occur. Secondary to leaching, doses of high fertility have in some cases been shown to overcome phytotoxicity of young herbaceous crops including germinated seedlings (Fig. 5B).
However, there are conflicting reports as to the role that fertilizer can possibly play in mitigating toxins, as it may be the leaching of the applied fertigation that is actually reducing the toxins. A combination of leaching and increased fertility can mitigate any negative growth, allowing for healthy plants to be produced in substrates with very high wood percentages (Fig. 5D).
As we continue to learn more about practical and cost-effective methods of reliably removing toxins from fresh hammer milled wood, as well as some sawdust and other wood industry by-products, it is likely that these cheap materials will be used more frequently as substrate components. As a result, these developments will drive the increased production of these cheaper wood products across the US (and in parts of Europe) which should keep costs low as a result of limited transportation distance and manufacturer/supplier competition.
And in the meantime, it should be noted that there are several commercial wood fiber products on the market that are toxin-free and available for immediate use.
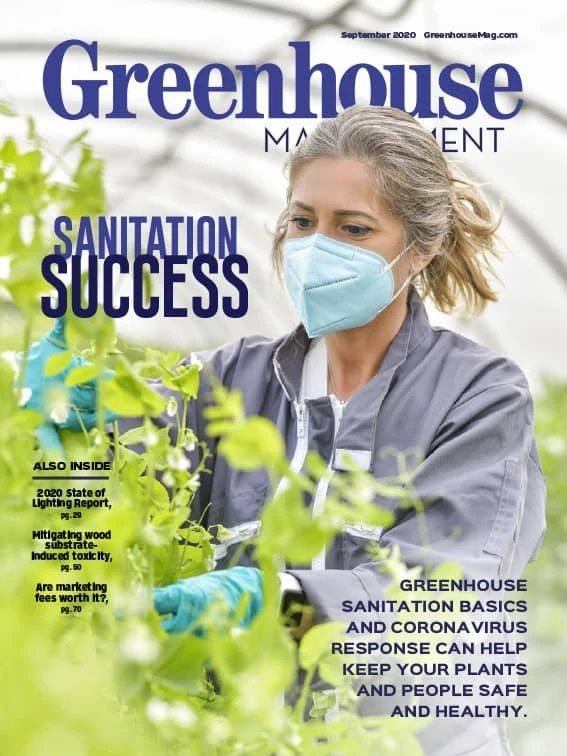
Explore the September 2020 Issue
Check out more from this issue and find your next story to read.
Latest from Greenhouse Management
- CEA Alliance celebrates bipartisan introduction of Supporting Innovation in Agriculture Act
- Dümmen Orange North America celebrating 25th anniversary in 2025
- Illinois Landscape Contractors Association changes name to Landscape Illinois
- 2025 Proven Winners Horticulture Scholarship applications now open
- ICL’s Gemini Granular herbicide now registered for use in California
- Eurazeo Planetary Boundaries Fund acquires Bioline AgroSciences
- Spring Meadow Nursery's Freedom Shelley finds joy in plants
- Leading Women of Horticulture: Dana Massey, Plantworks Nursery