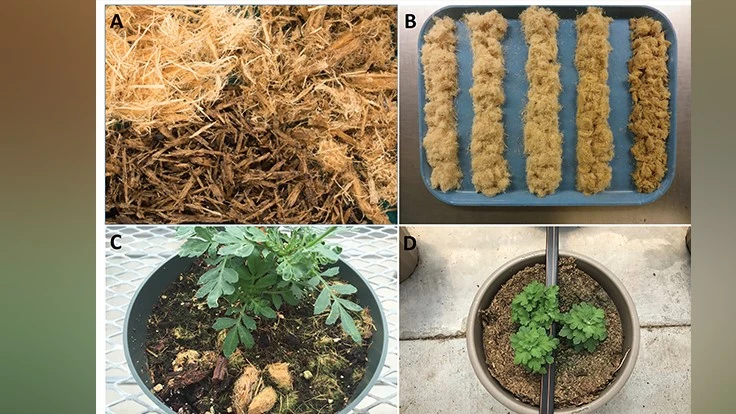

Water! Water! Water! Without doubt, one of the most valuable commodities on earth, water is a resource we must protect and respect in all aspects of our personal and professional lives. In container production systems, we have made tremendous advancements over the decades in water quality, water use efficiency, irrigation delivery methods and timing, water recapture/reuse/recycling, etc. Large multi-institutional projects (WateR3, for example), continue to innovate systems and educate growers on better water use technologies and management practices.
As new production practices and products enter the horticultural market, there is a continual need to evaluate and understand how water is utilized in these systems. Let’s take substrates for example. The development and use of “new” substrate materials, primarily wood products, has resulted in many growers having to relearn or rethink how they irrigate their crops. Of all the promises and potentials of wood substrate components in growing media, there are some adjustments that have to be made during crop production. In this article, we will highlight some of the things growers and researchers are seeing and learning relative to substrate hydration and wettability before and during crop production. But first, let’s review some of the common terms used (often incorrectly or interchangeably) to describe events and activities relating to substrate hydration and water.
Wettability — the preference and/or capability of a liquid (water) to be in contact with a solid (substrate). The interaction of fluids and solids
Capillarity — absorption and movement of water through/by capillary pores as a result of the forces of capillary action often against gravity. Also referred to as “wicking”

Evaporation — water loss due to vaporization that occurs on the surface of water as it changes into the gas phase. Can occur on substrate surface as well as container wall surfaces
Hydration efficiency — the ability of a substrate to capture and retain water in the fewest number of hydration events (water applications)
Hydraulic conductivity — the ability or ease with which water can move through substrate/soil pore spaces across a hydraulic gradient. Measured in saturated and unsaturated conditions
Water holding capacity — often referred to as “container capacity.” The percent volume of substrate pores filled with water after saturation and drainage. Maximum water holding capacity is rarely achieved in production, since irrigations do not saturate the substrate. “Maximum” substrate capacities are typically reported based on laboratory testing. “Achieved” water holding capacity is the amount of water held in containers after normal irrigation events that apply water on or in the containers. The achieved water capacity of a substrate after irrigation is most always less than the reported maximum water holding capacity.

Saturation — when all substrate pores are completely filled with water. Not achieved with normal irrigations (top or bottom) if drainage is allowed
Hydrophobicity — tendency to repel water; unable to be easily wetted. Refers to a substrate’s ability to be hydrated or rehydrated easily.
Hydrophilicity — tendency to be wetted by water with little or no difficulty.

Wood substrate products (fiber, chips, shavings, etc.) are now being offered by many of the largest substrate manufacturers in North America and Europe. It is projected that the number of wood products and commercial substrates containing wood will increase significantly in the next 18 to 36 months. There are three primary technologies (machine and process types) that create wood products: Disc-refiners, screw extruders and hammer mills (Fig. 1A). While there are variations within each of the processing types, the overall structure, particle size and shape and properties of wood products are fairly distinct. Regardless of the wood product, the moisture content of the material at the time it is incorporated with other components (like peat) will significantly influence how it blends and mixes. For example, a disc-refined wood fiber has visual and physical differences when wetted at different moisture levels (from left to right) of 25, 33, 50, 66 and 88% (Fig. 1B). The wetter the fiber, the more it clings and clumps to itself. When blended with peat, the clumps are difficult to uniformly blend with peat and can look (and function) unfavorably (Fig. 1C). Inadequate moisture content at the time of potting (not moist enough) can lead to shrinking and swelling of the substrate in containers (Fig. 1D) which can negatively affect water capture and movement during irrigation events.
During crop production, one of the most frequent comments from growers has to do with surface drying of substrates that contain wood products. The drying of the substrate surface is much quicker and more severe than the normal expected surface drying of peatlite mixes. The surface drying of substrates (Fig. 2A) containing wood is normally seen in late spring or summer production times when water use and demand (from the plant and from the surrounding environment) are greater. The quickness and severity of drying (and the resulting substrate color change) can often lead to premature irrigations and thereby overwatering issues during production. Just because the surface is dry it does not mean that there isn’t sufficient water in the container. The surface drying is a result of the wood particle sizes and shapes, the light and fluffy nature of the material (low bulk density), the very high air porosity and different hydraulic conductivity rates compared to peatlite mixes. During late winter or early spring production when water demand is lower, surface drying is rarely a problem and often times can remain wet and prone to algae growth (but no worse than traditional peatlite mixes) (Fig. 2B). This also occurs often in propagation substrates and systems.
As a result of container surfaces often drying faster than what is normally expected, it is important that the substrate be able to be rewetted sufficiently and easily. The wettability and hydration efficiency of wood products is a topic of much focus and interest at the moment. Substrate hydration is critically important at the time of substrate blending/mixing, at the time of pot filling, transplanting and throughout a plant’s production time.
There are many ways researchers and substrate manufacturers test substrates for their wettability, re-wettability, evaporative losses, need for surfactants, etc. At North Carolina State University, the two most common techniques we use to quantify these parameters are: 1) overhead/drip hydration efficiency test (Fig. 3B&C); and 2) capillary rise ebb-in-flood efficiency test (Fig. 3A). These techniques simulate different irrigation delivery methods to test the water capture, retention, movement and release in substrates. Based on wettability, hydration, capillary, etc., substrates can be better engineered, formulated and chosen to best function (in regard to water) based on the irrigation method, pot size and height, etc. of individual growers.
The addition of wood products (primarily fiber) has been shown to improve the wettability of peat substrates at low moisture contents. When dry, peat can be very hydrophobic and difficult to properly wet. Wood by itself is less hydrophobic and in some instances (based on fiber size) can be slightly hydrophilic. As an example, peat was tested at low (25%) and high (50%) moisture contents. Ten overhead irrigation events were applied to the substrate samples and the amount of water retained after each event was measured. After the 10 hydration events, the maximum water holding capacity of the samples was determined and are represented on the graphs (Fig 4A.) as the solid red lines across the top, while the water retention is plotted with the blue line. Peat by itself at 25% moisture only, had a maximum water capacity of 25% and the irrigation events never even got to that level. At 50% moisture, peat’s maximum water holding capacity increased to 68%, but yet again, the irrigation events were never able to achieve that capacity (Fig. 4A). When 10% (by vol) ForestGold wood fiber was added to the same peat materials, the water holding capacity increased in the dry peat to 58% (compared to 25% in peat alone) and at 50% testing moisture, maximum hydration was achieved after four irrigation events (Fig. 4B). Similar results were seen with Berger wood fiber (Hydrafiber) at both the 25% and 50% moisture tests (Fig. 4C) with maximum hydration occurring at the seventh irrigation event. Both wood products shown here are disc-refined materials. Other wood products produced with different methods or of different sizes can behave differently.
Current and future initiatives in the Horticulture Substrate Laboratory at North Carolina State University are focused on substrate-water-plant interactions. Research on irrigation water in container crop production systems is a three-pronged approach: delivery, movement and fate. Delivery encompasses the different means and methods of irrigating crops in indoor and outdoor production systems. The need for substrates to capture and retain water is a critical step in production efficiency. Water movement entails how water, once captured by the substrate, moves vertically up and down a pot and also laterally from side to side in a root ball/pot. Water movement can depend on irrigation delivery method (from top or bottom), size/height of container, substrate components, dryness or wetness of substrate at the time of irrigation, presence of wetting agent, etc. Water fate includes draining/leaching after irrigations, evaporation from the substrate surface, evaporation from the container walls (if non-plastic), bound in substrate particles unavailable to plants or transpiration from the plants themselves. Understanding water delivery, movement and fate as it relates to substrate properties and grower management practices will be critical in the future as more and more emphasis (and dare I say — regulations) will be placed on water usage and management. How can we engineer or formulate substrates to be better (more efficient) at capturing, moving and retaining water? How can we mitigate water loss from the substrate? How can we extend plant water availability in post-production environments to extend plant shelf-life and quality? Many questions. Many opportunities.

Explore the September 2019 Issue
Check out more from this issue and find your next story to read.
Latest from Greenhouse Management
- North Carolina Nursery & Landscape Association announces new executive vice president
- Plant Development Services, Inc. unveils plant varieties debuting in 2025
- Promo kit available to celebrate first National Wave Day on May 3
- Applications now open for American Floral Endowment graduate scholarships
- Endless Summer Hydrangeas celebrates 20 years with community plantings
- Invest in silver
- Garden Center magazine announces dates for 2025 Garden Center Conference & Expo
- USDA launches $2 billion in aid for floriculture growers