A properly designed grow facility is critical to success, and proper light design is a crucial component of that design. Properly designed lighting systems will evenly deliver the right amount of light to your garden.
Many grows utilize a lighting system that was thoughtfully designed and carefully put together to optimize light delivery to the garden. Others appear as if the lights were placed where they could easily be hung, not where they should be placed for maximum canopy coverage. Other grows pull too much power by installing too many lights, or their electrical load is not balanced properly across the electrical circuits within the facility. Grow light maintenance is often performed infrequently, if at all.
Here are some of the basic, and not-so-basic, considerations when planning your lighting systems to avoid common mistakes.

How much light do you need?
Far too often, conversations about lighting start with the same question: “How many of these lights do I need for an X-sized grow?” This is the wrong question to ask, as it does not address how much PPFD is required. (See the box below for an explanation of PPFD.) The proper question is, “How many of these lights do I need to achieve X PPFD in a Y-sized grow?”
Remember the 80/20 rule: Never exceed 80 percent of the total capacity of a circuit.
When it comes to how much light you need, most cannabis growers believe the sweet spot is approximately 1,000 PPFD to 1,200 PPFD for high light-tolerant cannabis plants in full flower — meaning this is likely strain specific — though research into this topic is far from complete. Early discoveries are also finding that some strains need much lower light levels, as little as 500 PPFD to 600 PPFD in some cases, so experimentation is required.
You also need to properly measure the photon output of the grow lights you plan to implement to ensure they are appropriate for your operation. The correct way to measure light output is with a quantum sensor/meter. There are several commercially available quantum meters with different sensitivity ranges, but some cut off at 660 nanometers (nm), thus missing the upper part of the PAR range (400 nm to 700 nm). Make sure the meter you select covers the entire PAR spectrum.
How many lights and at what height should you mount them?
Once you’ve determined what light levels you need, then you can determine the number of fixtures and mounting heights. These calculations are performed with the aid of a lighting design application and an IES (Illuminating Engineering Society) photometric file. IES files are created for lighting fixtures and are used to predict where every emitted photon will land. The exact room dimensions, bench heights and other components can be drawn in the application along with the light locations and heights to create a very informative “light map” of the grow space. Any good grow light manufacturer can help generate these light maps.
A clever lighting design is to deploy mobile benches even if your grow is a single level. If you were to take a quantum sensor/meter and measure the light levels in a typical grow facility’s aisles, you may find a lot of light is spilled onto the floor instead of being delivered to the plants. By deploying mobile growing benches and proper light design from your light map, you can produce an even and intense plane of light over the entire canopy when the benches are pulled together.
Whatever you do, never believe that power equals penetration. I hear it all the time: a 1,000-watt HID supposedly penetrates deeper into a plant’s canopy than a 600-watt HID, or an LED grow light with 5-watt emitters will penetrate deeper than one with 1-watt emitters. Unfortunately, this is not true.
Along with proper pruning/training techniques, light design will dictate penetration potential, not watts. Most of the photons that are exposed to leaf surfaces are absorbed; some go on to drive photosynthesis; others are quenched through various de-excitation techniques, such as being released as heat or fluorescence. This is why we see shadows of leaves on the ground regardless of lamp/emitter strength: It’s not the fixture directly overhead that “penetrates,” it’s the adjacent ones emitting at low-incident angles that make their way between the branches, deep into the plants.

Greenhouse lighting
With respect to greenhouse fixture design, I, too, used to fall for the idea that a perfect greenhouse fixture had to have the smallest possible physical footprint to minimize blocking sunlight. Greenhouses, especially in extreme northerly or southernly latitudes where they are often found, don’t suffer from having larger fixtures as much as you might think. In the winter, when the sun’s rays are low, sunlight can pass under the fixtures without leaving a shadow. These extreme latitudes also have intense summer light and heat loads that might potentially require shading or blocking for some portions of the day. Although it would take a very large fixture to block as much light as a cover, it does drive home the point not to worry too much about physical size and to focus on performance instead.
In every grow, monitor light levels at the end of rows. It’s common to see consistent light levels in the middle of the rows and see them drop off at the ends since there is no nearby fixture to add additional photons. To improve lighting at row ends, try lowering the end lighting fixtures or installing extra ones.
Electrical design
If you’re designing a new grow facility, work with an electrician to discover how much power you actually have entering the building. Adding additional power to a facility can be a very costly venture and, in some cases, cannot be done at all.
When your grow light design is mapped out and all the variables are known, add in estimated watts for other electrical equipment such as HVAC, inrush current (the surge of electricity consumed when an appliance is first turned on), general lighting and other equipment — including in the office — to know how much total energy you need.
Inrush current must be properly managed by either using one of many commercially available solutions to stagger the lights turning on, or by providing enough electricity for the peak (which is usually a more expensive solution). If you’re growing with dimmable power supplies (found in many LED grow lights) you might be able to use the dimming function to help mitigate large inrush currents by ramping the power to 100 percent over seconds to minutes.
Keeping your lights clean is the No. 1 maintenance task. It’s surprising how little buildup on a lamp/emitter can cause a measurable loss in light output.
Remember the 80/20 rule: Never exceed 80 percent of the total capacity of a circuit. For example, if you have a 20-amp circuit, don’t draw more than 16 amps on it. This simple concept can keep you from popping breakers, or worse, putting your facility at risk of an electrical fire.
The type of the power service matters too. A 240-volt dual (split) phase, the common power service in North American homes, might supply enough current to a small indoor grow/greenhouse, but 480-volt 3-phase, commonly used in industrial manufacturing facilities in North America, is needed to deliver the high-power demands of larger cultivation facilities. A 480-volt 3-phase provides more power with the same current because of its greater power density.
Personal story: I worked at a grow that had problems after an external transformer failed and took out some of the relays in one of the internal electrical panels. The electrician mentioned that room was pulling too much electricity, and that’s what likely caused the relays to fail. (There were no failures in the other rooms that were drawing the correct amount of power.) This caused several banks of lights to remain on 24 hours a day for several days. The problem was only discovered when the electrician entered the grow a few hours before the lights should have turned on to do some repairs. Thankfully the plants in that grow room were not negatively affected since they were within one to two weeks from being harvested. If this happened in a room that was early into the flowering phase, the results might have been quite different.
In every grow, keep an eye on light levels at the end of rows. It’s common to see consistent light levels in the middle of the rows and see them drop off at the ends.
Light maintenance

Just like everything in a grow facility, maintenance of your lights is required. Keeping your lights clean is the No. 1 maintenance task. It’s surprising how little build-up on a lamp/emitter can cause a measurable loss in light output. While you’re at it, make sure to clean your drivers or ballasts, especially any external heat sinks. Keeping them clean will help to keep them operating cooler, reducing the heat load in your rooms.
HID growers should have a lamp replacement schedule — somewhere between six months and a year, depending on lamp type and strategy. If a lamp fails and is replaced between scheduled replacements, make sure to track when and where it was changed. When you re-lamp the facility or an individual room, save any working bulbs. They can be used as spares in the next cycle. Murphy’s Law predicts that something will fail the evening before a long holiday weekend. Keeping spare ballasts, bulbs, drivers and/or arrays available can turn a stressful weekend into just a bit more work before leaving for the day.
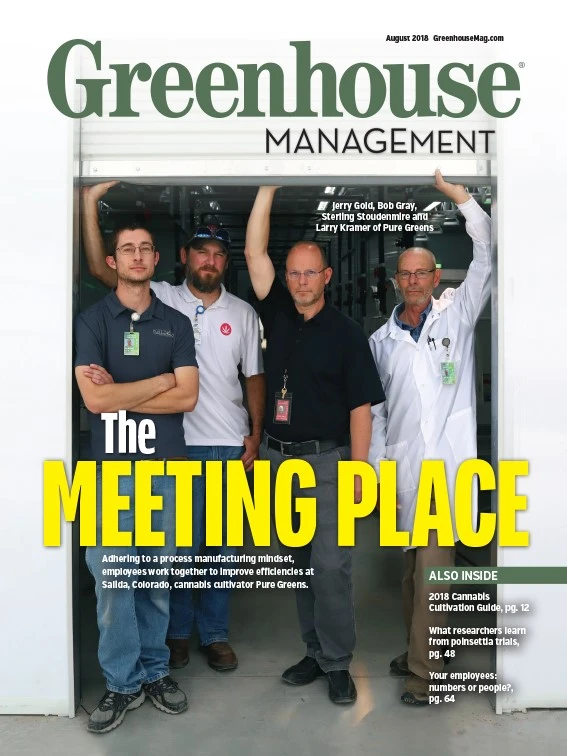
Explore the August 2018 Issue
Check out more from this issue and find your next story to read.
Latest from Greenhouse Management
- North Carolina Nursery & Landscape Association announces new executive vice president
- Plant Development Services, Inc. unveils plant varieties debuting in 2025
- Promo kit available to celebrate first National Wave Day on May 3
- Applications now open for American Floral Endowment graduate scholarships
- Endless Summer Hydrangeas celebrates 20 years with community plantings
- Invest in silver
- Garden Center magazine announces dates for 2025 Garden Center Conference & Expo
- USDA launches $2 billion in aid for floriculture growers