
After nearly 40 years in the greenhouse industry, you’d think Tom Samuelson would have already seen it all. But he’s still learning every day as new technologies, varieties, chemicals and materials keep him from getting bored.
“The industry is ever-changing. There’s still a lot I don’t know,” says Samuelson, head grower at Heartland Growers in Indiana. “I don’t think any two days are identical, which makes it interesting.”
Setting standards
Heartland supplies wholesale bedding plants and flowering crops to retailers throughout the Midwest. Samuelson regularly walks through Heartland’s 26 acres of greenhouses to “ensure growers are doing their jobs, producing the best crops possible for the scheduled week,” he says. He’s constantly observing whether mechanical systems are functioning properly, and whether plants are growing on schedule — then continually making adjustments to offset any issues or inconsistencies he sees.
For example, Heartland relies mostly on hand-watering — though automated boom irrigation and ebb-and-flow floors are also utilized. That means watering rates and techniques vary from one grower to the next, which means Samuelson has to adjust other application schedules accordingly.
“Some growers keep crops wetter, and then put more growth regulators on them. Other growers are a lot drier, so your growth regulator rates are going to change,” says Samuelson, who looks at PGR rates daily. “It’s ever-changing, because no two people water the same.”
Aside from regularly scheduled production, if there’s an issue with plant diseases or pests like thrips, Samuelson has to determine the right fungicide or insecticide for each problem. His knowledge of what works best in each situation is constantly expanding, as he trials new chemicals regularly. Plus, he interacts with the growers on his team every day to keep tabs on what they’re doing and what’s working.
As part of his responsibility to oversee chemical applications, Samuelson also implements the EPA’s Agricultural Worker Protection Standard (WPS) and other safety measures at Heartland.
“We’ve gone above and beyond the EPA standards to make sure everybody is protected when they’re putting on chemicals,” he says. “When you spray, you’re going to wear a mask, whether it says to on the label or not. Even if [the label says] just to wear rubber gloves and boots, you’re going to wear rubber pants, because I’d rather be too safe.”

Cultivating young growers
As Heartland’s head grower for the past six years, Samuelson works with a growing staff of about 20 year-round employees. They work in conjunction with the production team, which has around 60 employees at peak.
Finding talented growers to join the team is always a challenge. “There are more growers going out of the industry than coming in, which is tough,” he says. “There is a need for growers who are passionate about growing, dedicated to working long hours, and willing to grow new plants.”
Many interns and young growers quickly realize that they aren’t cut out for the greenhouse business. To those that make the cut, Samuelson emphasizes the opportunities available for growers to advance and excel in this evolving field. He’s passionate about passing down knowledge from more experienced growers to prepare the next generation.
“Wherever you’re at, you have different growers who all have different experiences. How can you get each grower to do their best and get more knowledge and learn from more experienced growers, to help them succeed?” Samuelson asks. “That’s what I’ve always loved to do, besides just growing.”
Managing the growing team is the biggest challenge of Samuelson’s job, he says — even more challenging (and rewarding) than managing busy plant production schedules.
Continuous improvement
Heartland continues to innovate and invest in new technologies and materials to keep up with production demands — which means even more change for Samuelson to manage.
Most recently, for example, Heartland switched from peat-perlite growing media to hydro fiber. Although it’s an adjustment from what he’s been using his whole career, Samuelson can already see the advantages.
When you spray, you’re going to wear a mask, whether it says to on the label or not. Even if [the label says] just to wear rubber gloves and boots, you’re going to wear rubber pants, because I’d rather be too safe.
Heartland also installed new flood floors last year, which help control the inconsistencies of hand-watering. Plugs now sit on convenient rolling tables, to help employees move young plants more efficiently. And a new sticking line automates the process of dibbling trays for cuttings, which used to be a manual process.
“When they invested in that, it paid back quickly,” Samuelson says. “I definitely see more consistency from item to item than before. That makes a difference how you grow it and how you water it, because if you change one little thing, there’s a rippling domino effect.”
As head grower, Samuelson’s job is to manage all those dominoes to keep producing high-quality plants on demanding schedules. The ongoing challenge of continually adjusting and improving this process is what Samuelson loves most about his role.
“It’s not like the big box stores are going to give you raises every year (for your product),” he says. “What can you do to help yourself? What can you do to improve your processes? It’s never the same as last year — and that’s the fun part.”
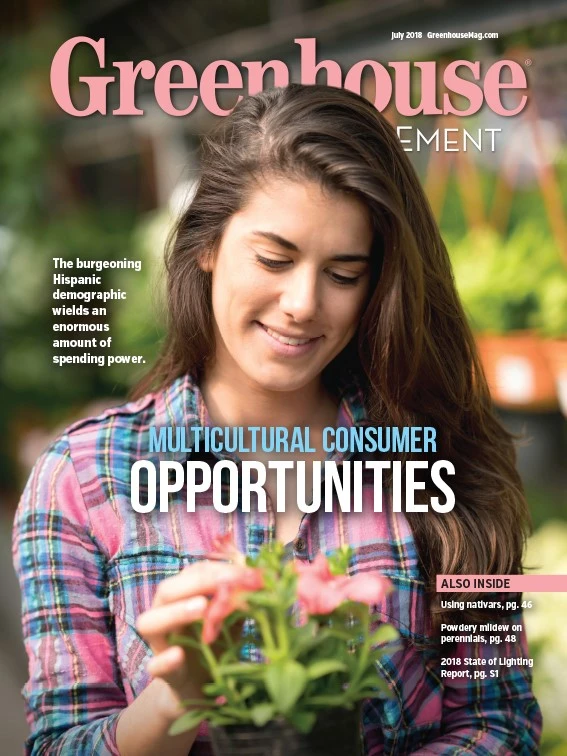
Explore the July 2018 Issue
Check out more from this issue and find your next story to read.
Latest from Greenhouse Management
- On the rebound
- A winning gameplan for spring
- Veseris expands in turf and ornamental with acquisition of Tessman and Lynde companies
- BioTherm launches Ultimate Grower Climate Control System
- Jess Lyga joins Bailey sales team
- Jimmy Toledo
- Green Gear: Work boots and long-range WiFi hub
- Pantone announces its 2025 Color of the Year